MX defines our range of high-capacity forage wagons that offer capacities from 33 m³ to 40 m³. Genuine dual-purpose forage wagons, they run in both the grass harvest chain as self-loading machines with discharge rollers and in the maize transport chain as forager-filled silage trailers. These machines score on versatility, reliability, efficiency and flexibility.
- Fully-featured dual-purpose forage wagon
- Articulated drawbar for high ground clearance
- Drawbar suspension for comfortable rides
- Camless pick-up, W-arrangement of tines
- Massive cut-and-feed rotor with wide Hardox tine plates
- Sloping chain-and-slat floor
- Steel structure and steel floor
- Pivoting headboard
Product video
KRONE MX – Self-loading and forager-filled forage wagon
The KRONE MX loader wagon impresses with its high efficiency and versatility. With its robust design, powerful chopping and feed rotor and generous loading volume, it is ideal for all operating conditions. Thanks to its simple handling and clever technology, the MX loader wagon guarantees optimum forage quality and high transport performance. Its durability and ease of maintenance make it the perfect choice for any farm.
Product features
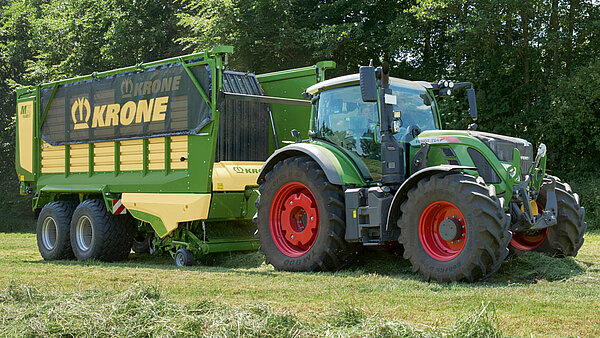
- Fully-featured dual-purpose forage wagon
- Articulated drawbar for high ground clearance
- Drawbar suspension for comfortable rides
- Pick-up unit without cam track with w-shaped tines
- Large cutting rotor and feed rotor with wide Hardox steel plates
- Steel structure and steel floor
- Pivoting headboard
- Sloping chain-and-slat floor
MX, this is the designation for high-performance large-capacity loading and forage transport wagons with a transport volume of 33 m³ to 40 m³. Genuine dual-purpose forage wagons, they run in both the grass harvest chain as self-loading machines with discharge rollers and in the maize transport chain as forager-filled silage trailers. These machines score on versatility, reliability, efficiency and flexibility.
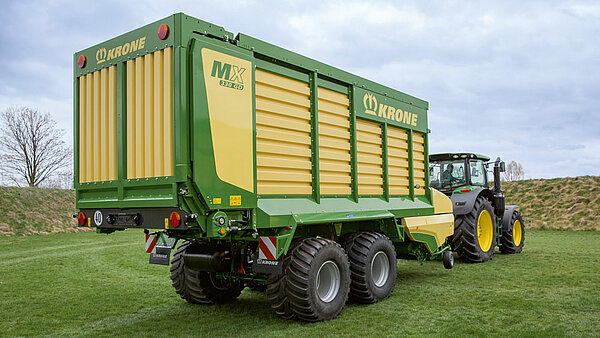
- Self-loading and forager-filled forage wagons
- All-steel body with 33 m³ loading volume
- Hydraulic crop guide flap on the front wall of the loading space
- Unloading with or without discharge unit
- Cutting rotor with 41 blades
The robust all-steel body with 33 m³ loading volume and the large tandem chassis with steered rear axle make the MX 330 a genuine loading and forage transport wagon. The machine is available with discharge rollers (GD) and without the rollers (GL). A hydraulically operated silage hatch at the top of the headboard is standard-fit for easier filling from the leading forager.
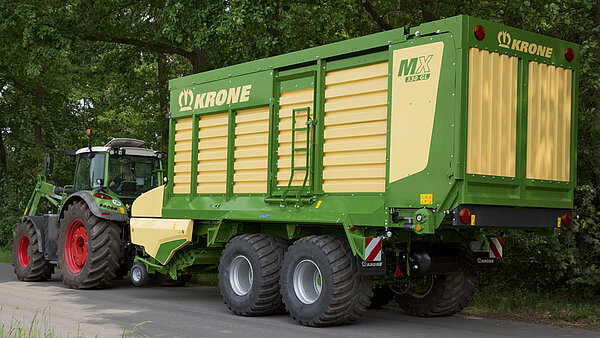
The long and slim drawbar, the compact build, and the tandem axle with either a steered rear axle or a mechanical force-steer option optimize ride performance and stability – both in the field and on public roads.
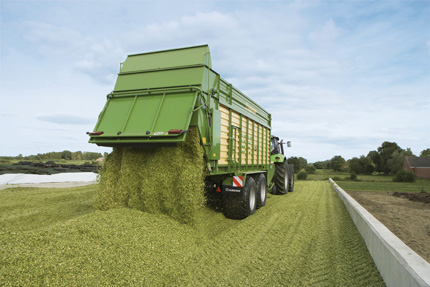
The MX 330 GL/GD as forager-filled wagon: Its rugged steel structure and the high 18t axle load make the MX 330 the most reliable and productive companion for the forage harvester.
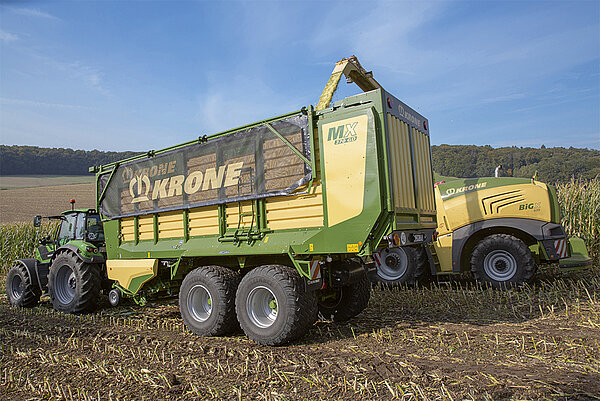
The MX 330 GL/GD as self-loading wagon: Fast and consistent fills are key and attributed to the wide work width of the pick-up and the cutting rotor as well as the wide and short feed chamber. Blades with wavy edges and plated rotor tines ensure a particularly high quality of cut.
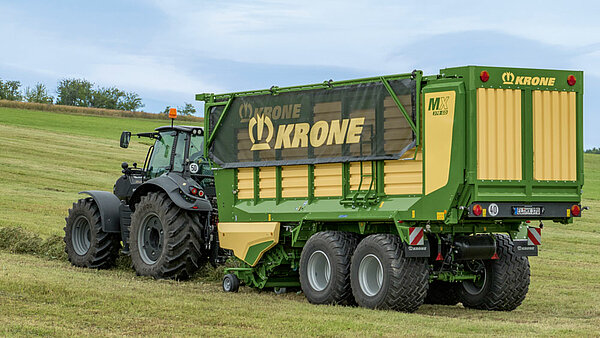
- Self-loading and forager-filled wagons
- 37 m³ or 40 m³ capacities
- The all-steel machine is available with and without discharge rollers – as GD or GL version
- Hydraulic pivoting headboard
- Rotor cutter with 41 blades
The two dual-purpose forage wagons MX 370 and MX 400 feature the proven designs and innovative technical solutions of the RX series as the base for implementing new and practical ideas.
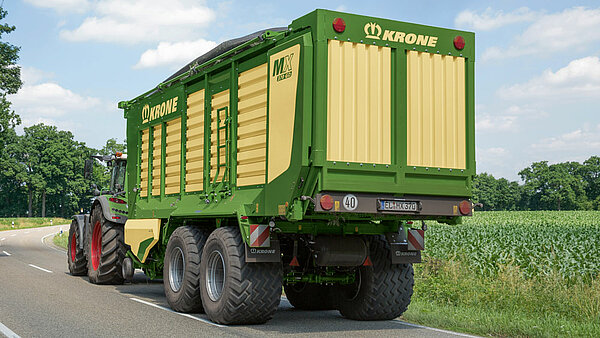
The long and slim drawbar, the compact build, and the tandem axle with either a steered rear axle or a mechanical force-steer option.
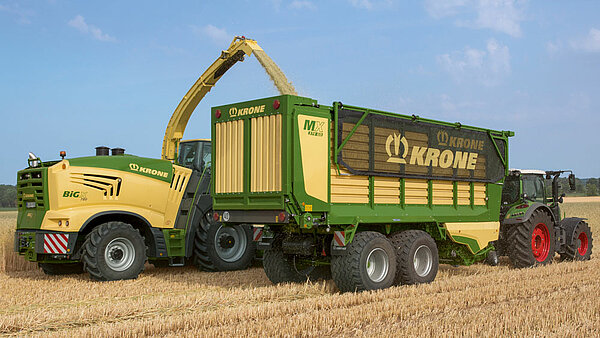
Serving as forager-filled trailers: Offering capacities of 37 m³ and 40 m³ and a high gross weight of up to 22 t, the MX 370/400 models make perfect silage trailers that unload the material extremely fast. This dual use option makes MX an even more productive machine.
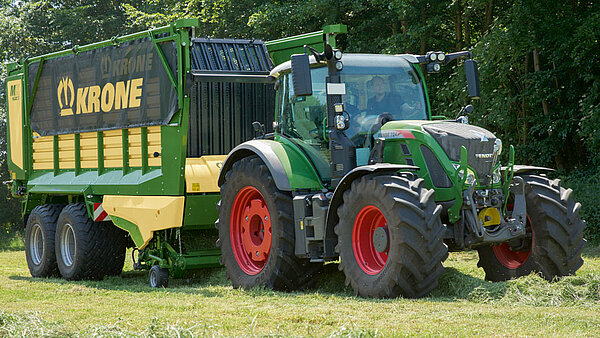
Serving as self-loading forage wagons: The extra wide pick-up unit, the wide feed chamber and the hydraulic pivoting headboard ensure fast and consistent fills to maximum capacity. For a superior cutting quality (scissor-like cuts), the gap between a blade and a feeding tine is extremely small.
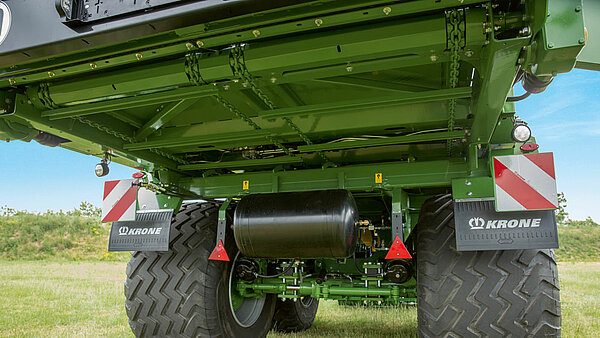
- Standard ball hitch for bottom attachment
- Articulated drawbar for high ground clearance
- Drawbar suspension for comfortable rides
Varying conditions, high payloads, challenging unloading sites and long-distance travel at speed are challenges that call for a very stable, safe and shockload cushioning running gear. It is down to the steered tandem axle, the ball hitch and the articulated drawbar that the MX is up to any job and situation.
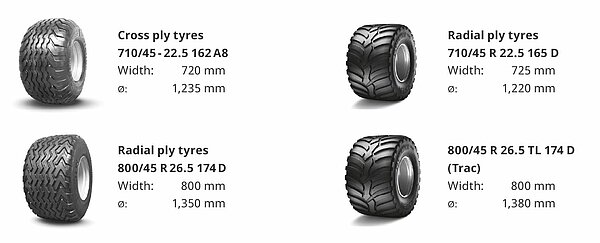
A range of tyre options is available in the following sizes to suit all harvest conditions: 710/40 R 22.5, 710/45 R 22.5, 710/45 R 26.5 and 800/45 R 26.5.

The forced steering on the rear axle makes it easier to drive bends and reduces scuffing and tyre wear. The system is set up and monitored by means of pressure gauges. An electronic power steering system is also available which allows operators to intervene when working in sloping fields or on the clamp for example.
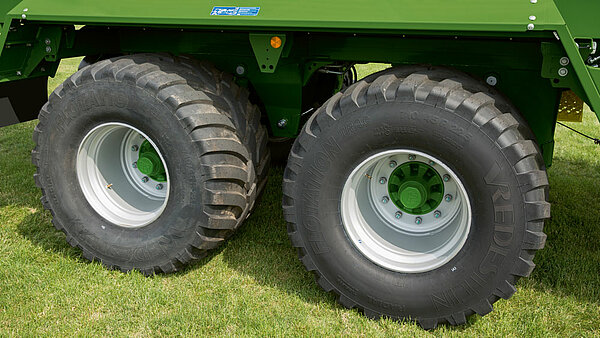
The MX runs on tandem axles with mechanical suspension as standard specification. A hydraulic levelling system is available as an option. The system ensures the weight is always distributed uniformly to all four wheels to give optimum rides and stability. A range of tyre options is available to suit all harvest conditions.
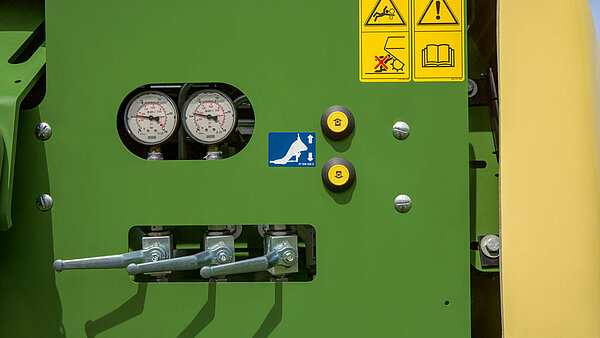
For easy attachment and removal, the articulated drawbar is raised and lowered by pressing a button on the machine.
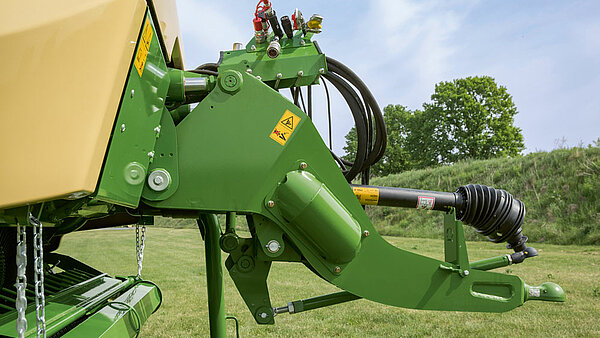
The MX masters even narrow bends. Its long, slim and suspended drawbar is articulated and cushions the shockloads. Two massive rams lift the drawbar no matter the load and give the wagon plenty of ground clearance no matter the situation. As an option, an automatic system stores and retrieves the two drawbar positions automatically.
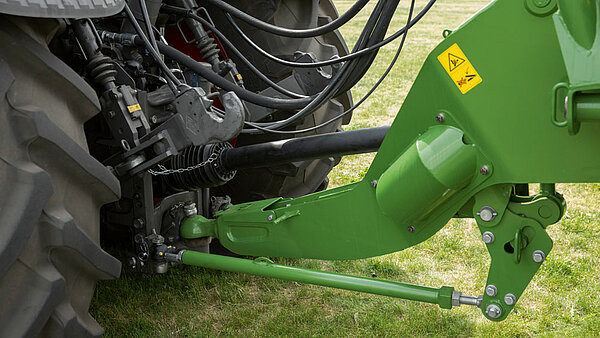
All MX models are specified with the standard ball hitch 80 which offers a tongue load of 4 t, a level of specification that accounts for hard wearing and maximum manoeuvrability. Mechanical force-steering is available as an option. Simply attach the steering rod to the ball 50 and the tractor.
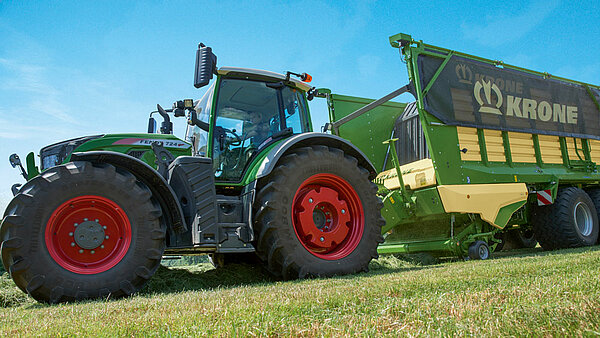
- Wide pick-up for clean and comprehensive gathering
- No cam track means few moving parts, minimized service and maintenance and quiet running
- 6.5 mm thick double tines with large coil diameter
- Tines arranged in a ‘W’-line
The EasyFlow pick-up excels by virtue of clean and thorough gathering – at high work rates and at low wear rates even in difficult conditions. Made up of few moving parts, the unit runs extremely quietly and dependably.
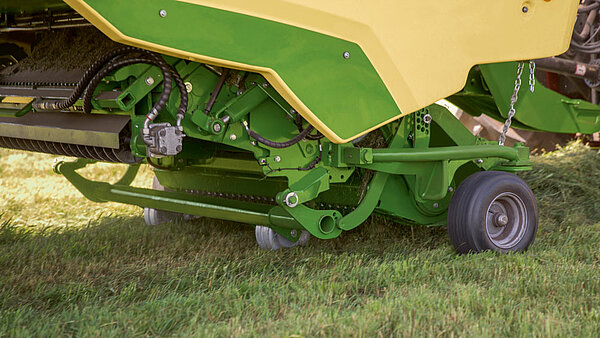
The pick-up runs on two castering gauge wheels which pivot flexibly. These wheels are height adjusted without tools and can be complemented by two extra and optional gauge wheels at the rear. These extra wheels do not run in the tractor wheelings and help contouring in difficult harvest conditions and reducing crop contamination.
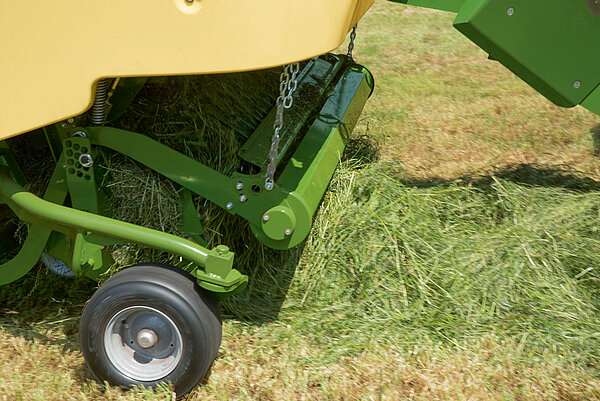
The crop press roller supports the pick-up in gathering the material effectively. Its height is adjusted easily and without tools to match the current crop, the swath volume and ground speed.
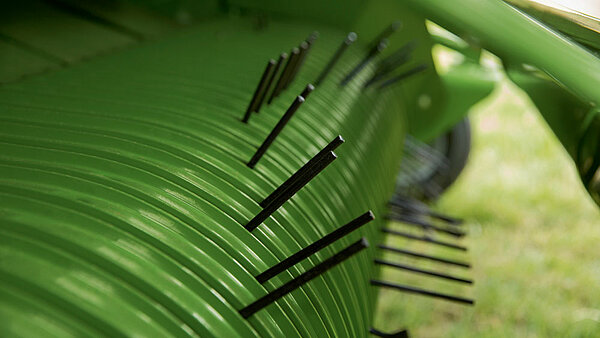
The 6.5 cm diameter double tines with large coils are particularly hard-wearing. Arranged in a wavy pattern, six rows of tines feed the material from the ends to the middle of the rotor, thereby preventing crop from building up as the machine travels through bends for example and spreading it evenly across the full width of the cutting rotor.
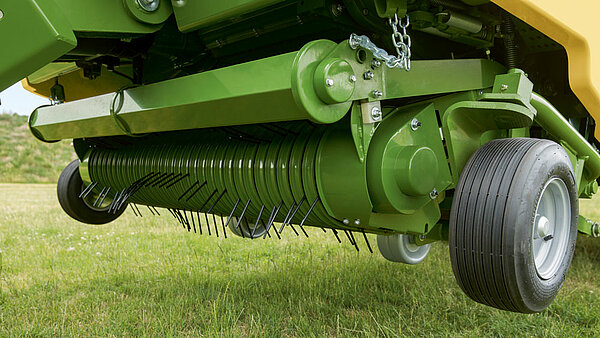
Working at a width of 1.8 m (to DIN 11220), the pick-up gathers also wide swaths no problem and feeds the material to the cutting rotor in a very consistent flow. Spring-suspended and pivoting, it excellently adapts to ground contours.
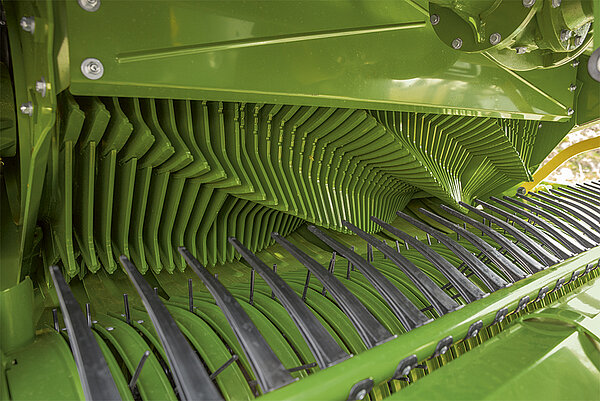
- High loading capacity thanks to wide rotor with large diameter
- Smooth running thanks to rows of tines arranged in a spiral
- Easy pulling blades for exact and scissor-like cuts
Powerful and low-maintenance, the MX rotor operates very smoothly and feeds the crop super gently and consistently into the machine. The rotor blades give exact cuts, stay sharp for a long time and are very easy to replace.
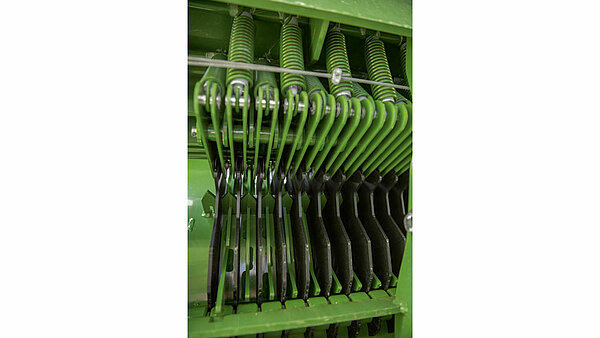
Each blade is individually protected by a tensile spring, the tripping force of which can be adjusted centrally and steplessly. After the blade has tripped, it resumes automatically its cutting position.
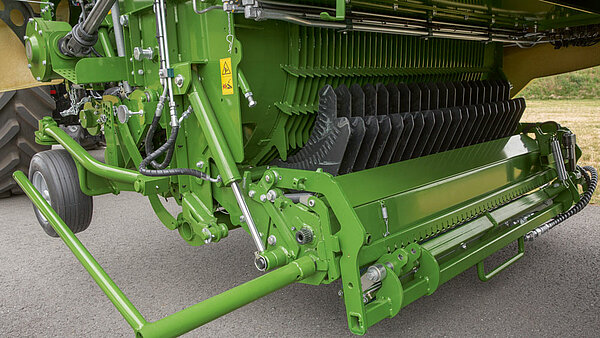
The central blade group control system controls the cutting length. Operators can select 41, 21, 20, or 0 blades, with 41 blades achieving nominal chop lengths of 37 mm. 0 blades means the system is not cutting.
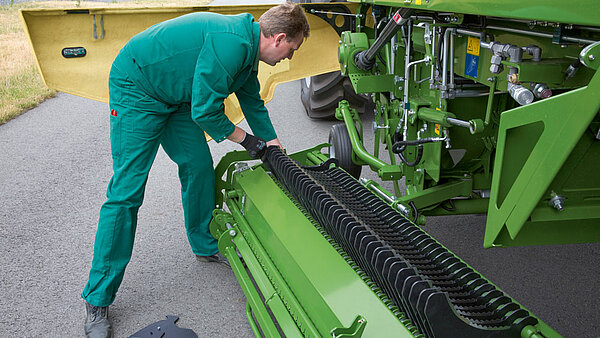
The blade cassette lowers hydraulically and swings out to the side. After the blades are unlocked on a central lever they are removed and swapped conveniently.
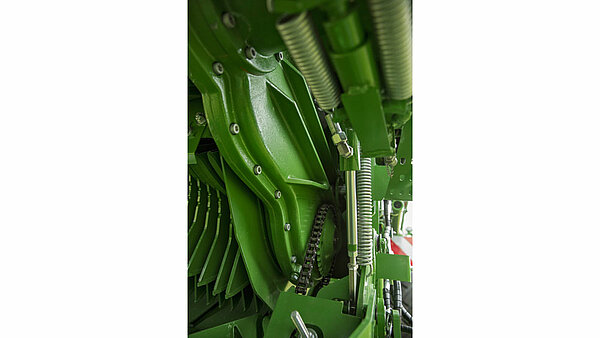
The rotor is driven by a massive and enclosed spur gear. The rotor is driven by a massive and enclosed oil-immersed spur gear capable of withstanding extreme strain.
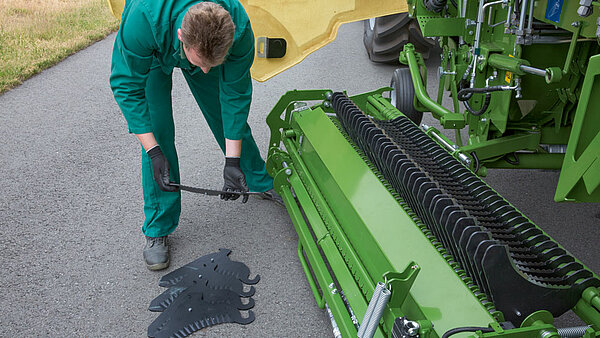
The blades have long cutting edges which give particularly light-pulling cuts. The wavy edges give cut very precisely and maintain their sharpness for many operating hours. All blades are identical and interchangeable.
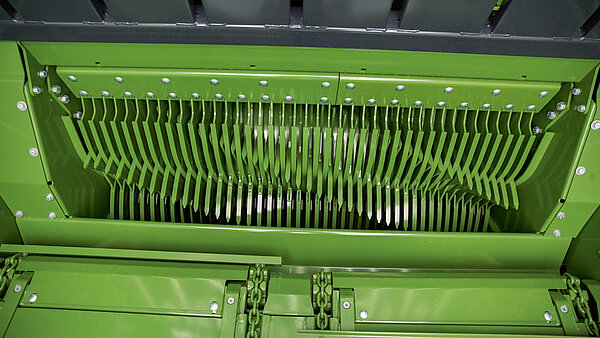
The rotor cutter measures 880 mm in diameter and offers a working width of 1,580 mm to handle large amounts of material. The eight rows of helical 17 mm tines have Hardox plates for long service life. The scraper elements, too, are made from hard-wearing Hardox steel. The design ensures the tines feed the crop dependably through the blades for precise and scissor- like cuts and fast and uniform fills.
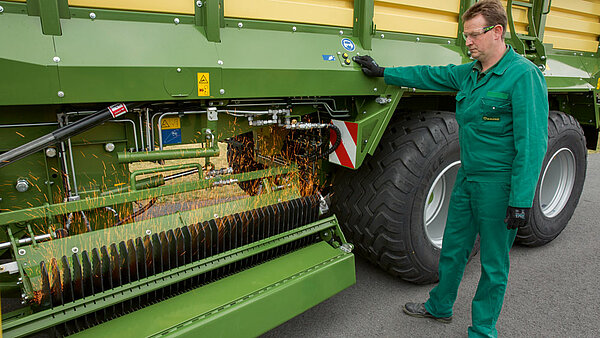
- Convenient and quick sharpening of the blades
- Sharpening 41 blades takes less than four minutes
- Gives all blades a consistent grind
- Reduces fuel consumption and improves the forage quality
The automatic SpeedSharp blade grinder sharpens your blades in just a few minutes. Grinding the blades right on the machine and on the site gives you great flexibility and saves time you would otherwise spend on replacing dull blades – an important detail when your aim is consistently high-quality forage and good fuel economy.
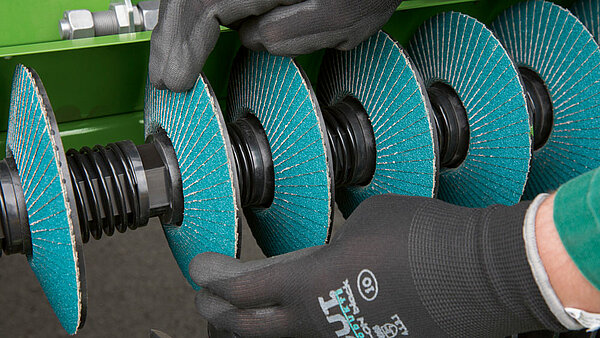
Each grinding disc is pressed on to the blade by a bevel spring for a high-quality and consistent cut to each individual blade at minimum material wear.
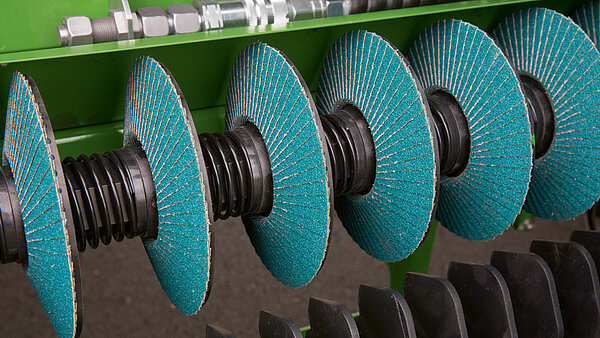
The discs have flaps that overlap generously to ensure superior grinds and longevity, giving a 'cold' grind that cuts out the risk of annealing.
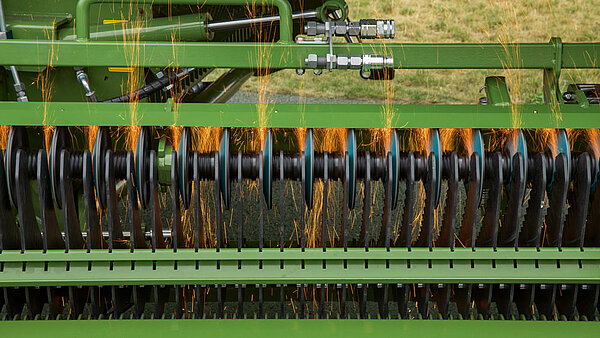
Grinding 41 blades takes less than four minutes. As grinding takes place, the sparks can fly off without doing any harm to the machine.
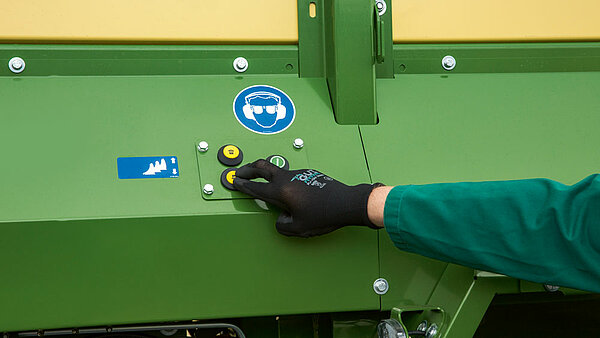
The blade cassette and the blade grinder are operated conveniently by pressing a button on the machine.
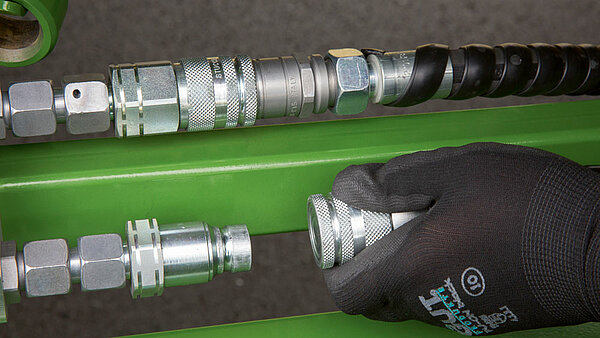
Two hydraulic lines are coupled to the on-board chest to make the connection to the grinder drive.
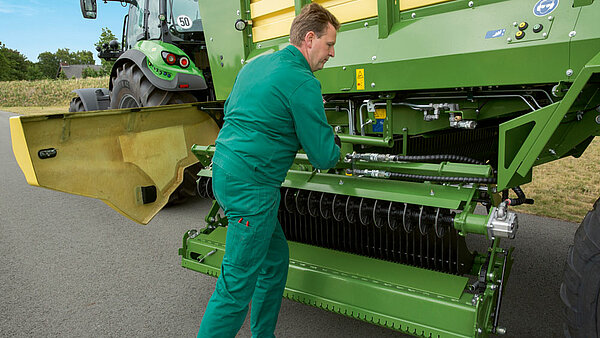
To get ready for grinding, pull out the blade cassette and swing it alongside the machine. The grinder folds up and into position above the blades, which are then fixed in place with the retaining comb.
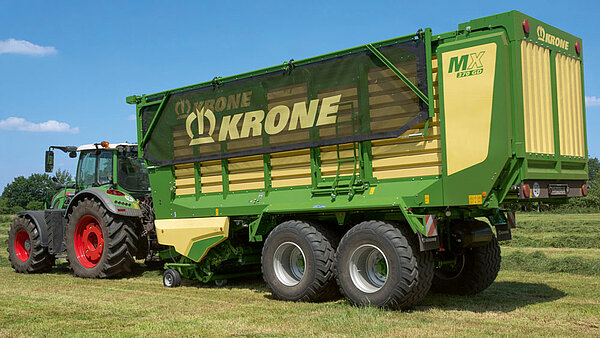
- Steel structure and steel floor
- Pivoting headboard
- Double scraper conveyor, sloping towards the front
- With or without discharge rollers
- Optional cross conveyor belt for unloading fresh feed in the barn
The MX dual-purpose loading and forage transport wagons are designed with an all-steel loading space for the toughest practical applications. The pivoting headboard makes for easier filling – both from the forage harvester or the pick-up. The heavy-duty chain-and-slat floor feeds even heavy forage swiftly and consistently to the rear for unloading.
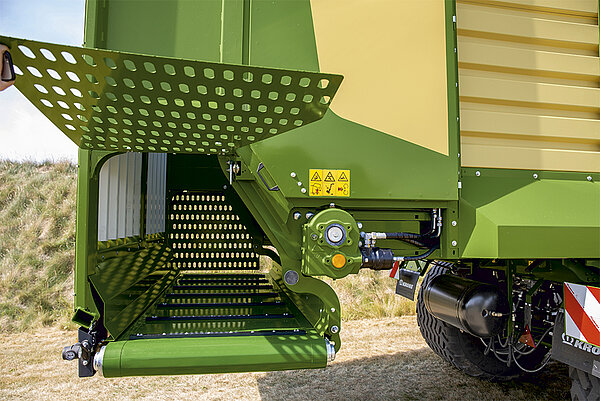
The optional cross conveyor belt is an ideal feature for farmers who feed the fresh forage directly to their cows. The 90 cm wide belt feeds the material to the right and left side. But you can also empty the machine as usual via the discharge rollers without any previous modification. The belt is integrated in the “rucksack” tailgate and moves out of the way when this is opened.
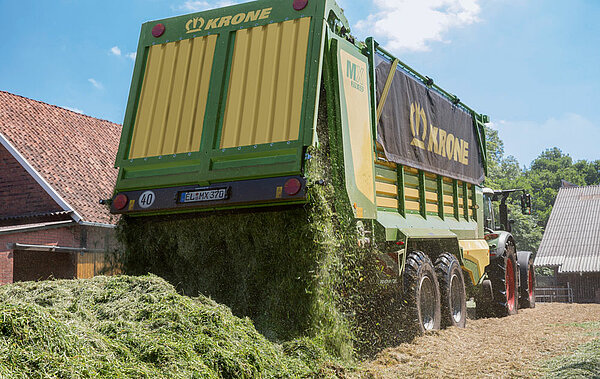
The discharge rollers unload the material in very uniform layers. Available in sets of two or three, the bottom roller spins at a higher speed than the top roller(s).
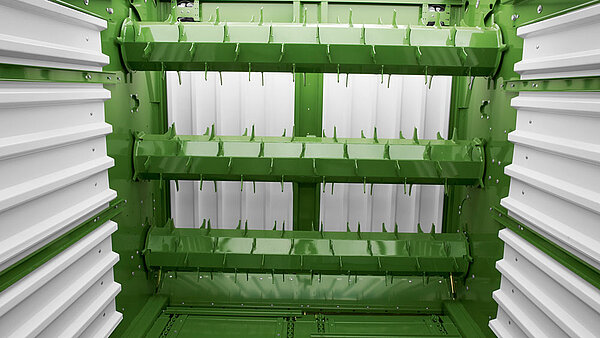
The MX GD models have two or three discharge rollers which unload the material in a uniform mat. Overload protected by the clutch in the main driveshaft, the rollers discharge the material fast and efficiently.

The machine can be specified with optional sensors that enable and control the chain-and-slat floor. The PowerLoad sensor measures the pressure that is exerted by the material on the headboard (right) while another sensor at the top of the headboard scans the current angle of the silage hatch (left). The chain-and-slat floor is started automatically as soon as the pressure scanned equals the preset pressure. Depending on the crop, is also possible to use the two sensors independently of each other.

The four floor chains are made of high-tensile tube steel and the slats are made of channel steel. The chains are driven by two hydromotors – one on either side of the machine – and convey the heaviest material fast and effectively to the rear for quick unloading. The floor slopes at its front end, thereby shortening the passageway into the machine and reducing the strain on the crop as well as input power whilst boosting the intake rate.
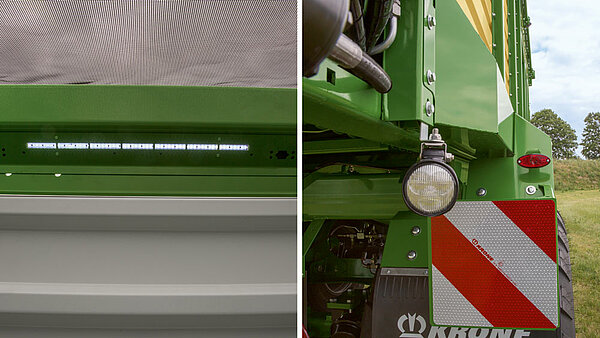
It is possible to order optional LED lights for the MX models which can be fitted on the inside and outside of the body. The inside is illuminated by four optional LED light bands that are installed at the top of the sides while up to four LED work lights can be installed on the outside for better visibility. All lights can be switched from the operator terminal.
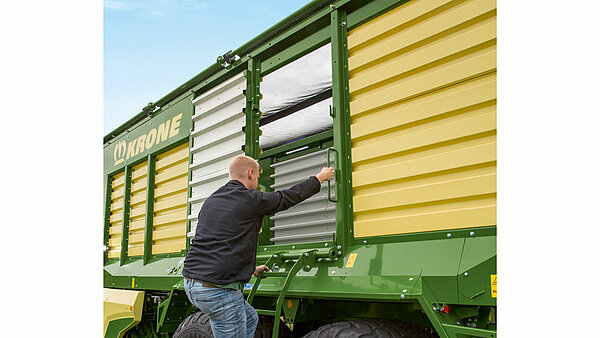
Those MX forage wagons that are fitted with discharge rollers have a large nearside door that gives access to the load area. After you climb the fold-down ladder with a handle on the side for safe ascent.
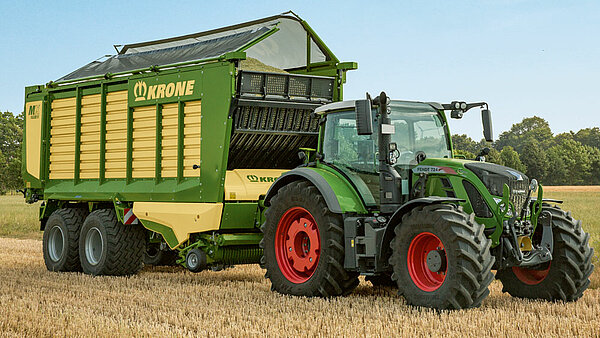
After the machine is filled to capacity, you can protect the material with a pair of crop covers to prevent losses during road travel. The covers are made of high-tensile texture and are operated by two hydromotors that are controlled from the cab-based terminal.
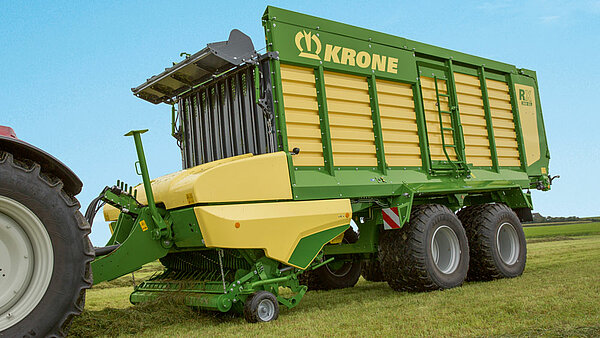
The straight headboard on the MX 330 has the hydraulic top hatch as a standard feature. Opening a field, the operator can open the hatch conveniently from the cab for an improved crop flow into the machine.
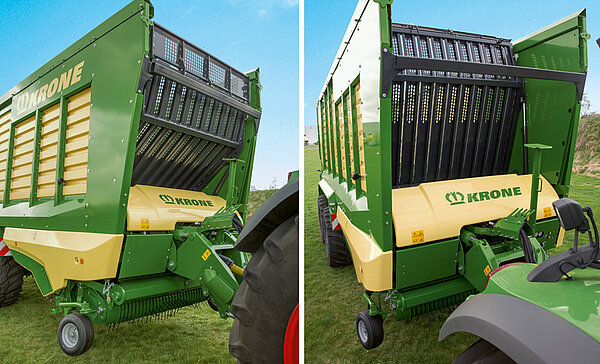
The MX 370 and 400 models have a hydraulic headboard which pivots to various positions to support the filling and unloading processes. For example, when the machine is filled by a forage harvester, the headboard pivots all the way forward to maximize the capacity (left). By comparison, when the machine is gathering material through the pick-up, the headboard is nearly vertical to optimize the filling process. Once the loading area is filled to capacity, the headboard pivots towards the tractor to expand the capacity by 4 m³. To speed up unloading, the headboard can pivot back and forth and support the work of the floor chain.
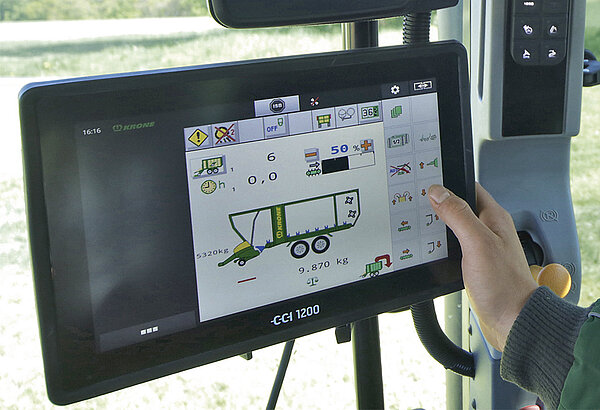
- Clear and convenient
- Easy and user friendly
- ISOBUS compatible
Working with the KRONE comfort on-board electronics significantly simplifies, improves and speeds up work with the MX dual-purpose loading and forage transport wagon. Two different terminals are available to cater for different applications and needs.
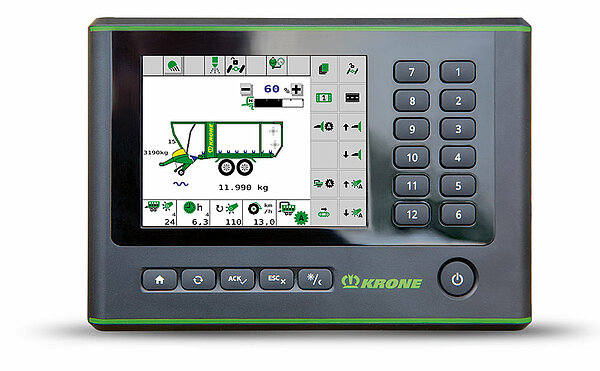
[Translate to EN:] Das kompakte DS 500 Terminal verfügt über ein 5,7"-Farbdisplay. Die Bedienung erfolgt wahlweise über die 12 Funktionstasten, per Touchscreen oder mithilfe des Scrollrads auf der Rückseite. Die Verwendung eines optionalen Joysticks macht die Bedienung noch komfortabler.

More operator comfort: The CCI 1200 operator terminal with 12-inch touchscreen off ers the same features as the Delta terminal plus it allows operators to split the screen in two views, for example to see all machine control elements in one view and the camera footage in the other. Also, an additional UX joystick enhances operator comfort even further.
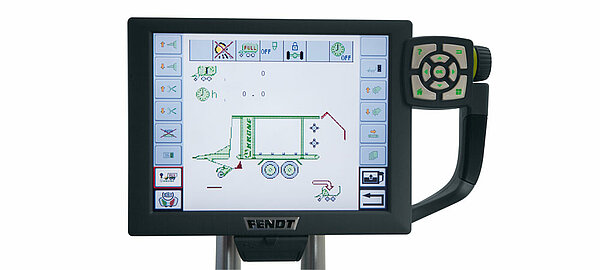
Existing third-party terminals: If the tractor has an ISOBUS terminal, you can use this to control the electronic system on MX. In this case, there is no need for a KRONE terminal and operation is even more convenient.

DS 100 control unit: The layout of the DS 100 control unit is specially designed for the convenient operation of a forage wagon, providing optimum ergonomics and haptic press button feedback to the operator so they can now use the keypad without looking down.
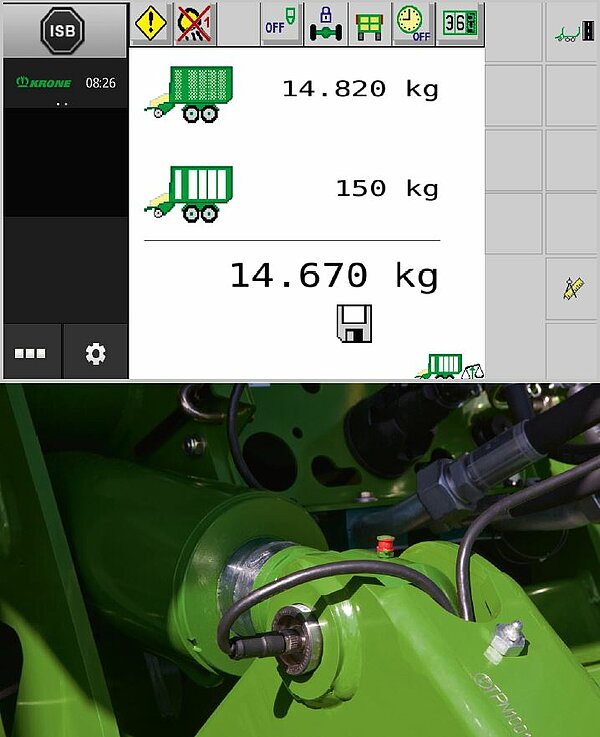
The optional weighing system uses sensor pins on the chassis and on the articulated drawbar to determine and store the weight of the load.
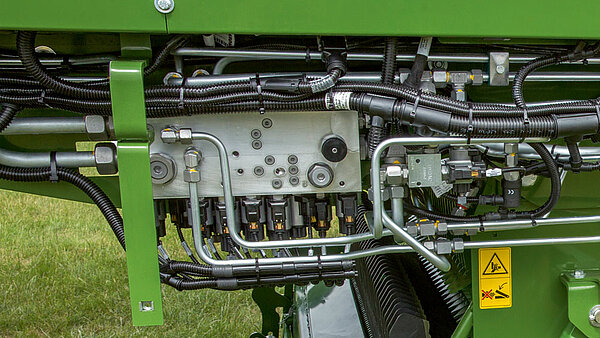
The comfort hydraulic system is loadsensing-compatible, which means, if hitched to a load-sensing linkage, oil will be supplied only on requirement. This reduces the load on the tractor hydraulics. On tractors without loadsensing it is also possible to operate the machine via the constant pressure hydraulic system.
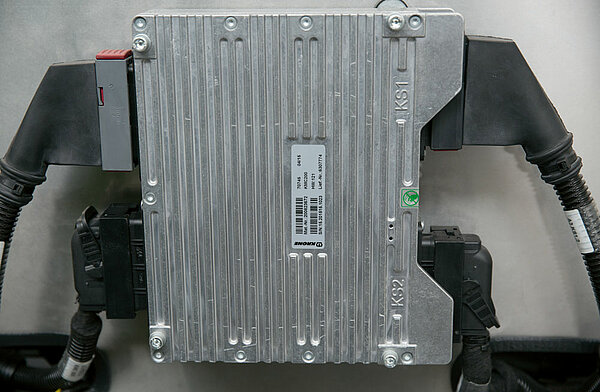
The Comfort electronic system is ISOBUS compatible and is required for the optional features such as the automatic loading / unloading system.
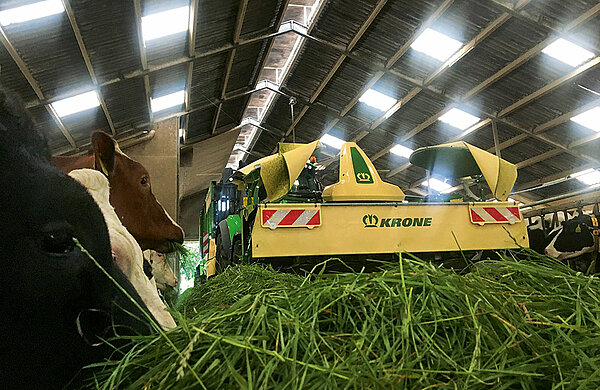
The combination goes into narrow buildings and feed passages thanks to the patented slewing gearbox which allows the wide mower to be folded into a narrow unit.
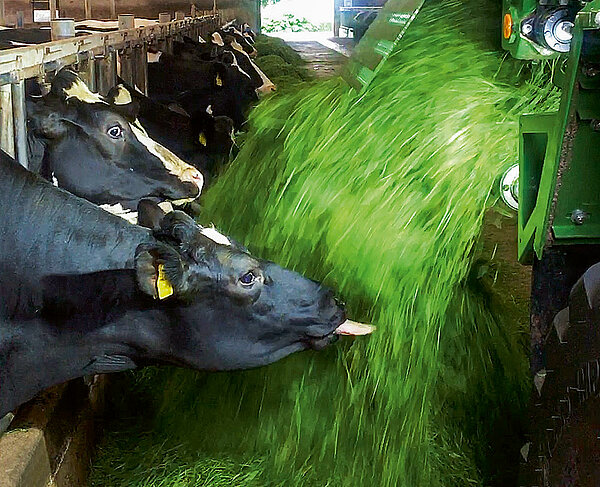
The cross belt discharges the feed on to small and large any feed passages in no time. Mounted cleverly at the tailgate, the discharge belt enables owners to use the MX for feeding fresh grass directly to the cows.
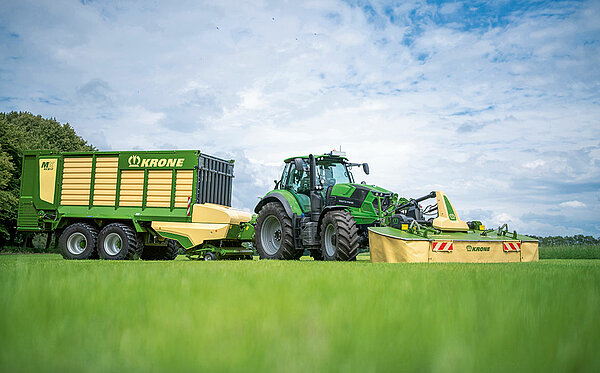
[Translate to EN:] Für noch höhere Milchleistung aus dem Grundfutter gewinnt die Frischgrasfütterung zunehmend an Aufmerksamkeit. Steigende Lagerkosten von Silagen, Heumilchprogramme und andere treibende Faktoren lassen die Frischmassefütterung in neuem Licht erscheinen. KRONE bietet hier genau die passenden Maschinen, um täglich wertvollstes Futter zu bergen. Das EasyCut F 400 CV Fold in Kombination mit dem MX 330 GD bietet hier maximale Schlagkraft.
Models
MX 330 GL | MX 330 GD | MX 370 GL | MX 370 GD | MX 400 GL | ||
---|---|---|---|---|---|---|
Designation | loading and forage wagon | loading and forage wagon | loading and forage wagon | loading and forage wagon | loading and forage wagon |
configure
|
Capacity (m³) | 33 | 33 | 37 | 37 | 40 |
configure
|
Pick-up working width (m) | 1.80 | 1.80 | 1.80 | 1.80 | 1.80 |
configure
|
37 | 37 | 37 | 37 | 37 |
configure
|
|
No. of discharge rollers | - | 2 / 3 | - | 2 / 3 | - |
configure
|
Power requirement (kW/hp) | 88 / 120 | 88 / 120 | 103 / 140 | 103 / 140 | 103 / 140 |
configure
|
configure
|
configure
|
configure
|
configure
|
configure
|