RX is KRONE’s latest generation of forage wagons. Offering capacities between 36 and 43 m³, these machines serve two purposes – as self-loading and as controlled-unloading forage wagons but also as silage trailers in the transport fleet serving the forage harvester. The optional 30.5-inch tyres offer a higher load bearing, easier pulling, better soil protection and enhanced road safety. This versatility is paired with an outstanding reliability and efficiency, making the RX a particularly productive machine.
- Articulated drawbar for high ground clearance
- Drawbar suspension for comfortable rides
- Camless pick-up, W-arrangement of tines
- Swing-out cutterbar with 46 selectable knives
- Massive cut-and-feed rotor with wide Hardox tine plates
- Greater capacity from pivoting headboard
- Double chain-and-slat floor slopes at front
- Steel structure and steel floor
Product video
KRONE RX – Self-loading and harvester-filled forage wagon
Offering capacities between 36 and 43 m³ (DIN 11741), these wagons are not only self-loading but can control the unloading rate and serve as silage trailers in support of the forage harvester. This versatility is paired with an outstanding reliability and efficiency, making the RX a particularly productive machine.
Product features

- OptiGrass
- Camless pick-up with hydraulic drive with hydraulic relief
- Integral rotor and SplitCut for optimum conditioning – provides a perfect cut
- Blade cassette can be swivelled out to the side with 40 or 54 individually protected blades
- Optional SpeedSharp blade grinder
- Pivoting front wall increases capacity from a compact build
- Axle assembly for maximum comfort
- Premium lighting Standard
- Options, which are worthwhile!
KRONE RX – the efficient loading and forage transport wagon a transport volume of 33 to 40 m³. The dual-purpose loading and forage transport wagon truly fulfills the requirements of both its purposes: as a loading and forage transport wagon in the grass harvest chain and as a forager-filled silage trailer in the maize transport chain. With the high-performance 'OptiGrass 28 and 37' cutting systems, it offers a clean, precise cut as well as structured and homogeneous forage conditioning across the entire width. Thanks to its versatility, operational reliability and high efficiency, the use of an RX wagon is particularly economical.
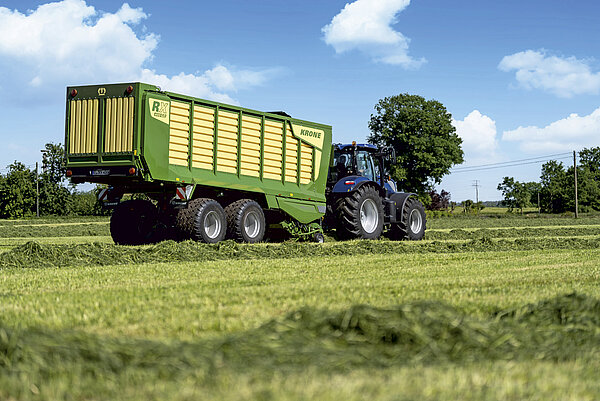
- Loading and forage transport wagons
- 33, 37 or 40 m³ loading volumes
- Compound running gear (RX 330 /370)
- Hydraulic running gear (RX 400) available for all models as an option
- Unloading with or without discharge rollers
- OptiGrass concept for a clean 28 or 37 mm cut
Their proven-and-tested design features and innovative technologies, such as the KRONE SplitCut edge cutting system and the OptiGrass concept, make the RX dual-purpose loading and forage transport wagons the ideal machine for efficient harvesting. With a loading volume of 33, 37 or 40 m³, these loading and forage transport wagons offer ample capacities for successful forage harvesting.
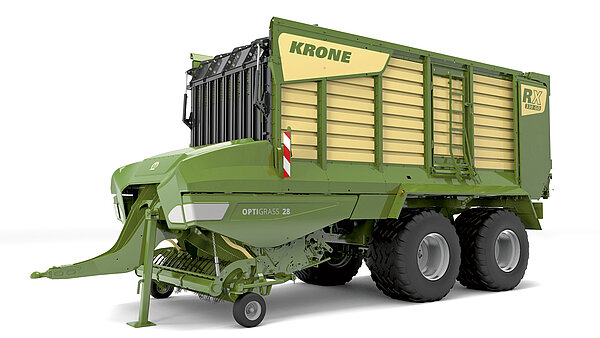
[Translate to EN:] Die Modelle RX 330 und 370 sind serienmäßig mit einem Verbundfahrwerk ausgestattet. Optional erhältlich ist auch ein hydraulische Fahrwerk welches beim Modell RX 400 serienmäßig geliefert wird. Beide Fahrwerksvarianten bieten eine perfekte Kombination aus Stabilität, Agilität und Komfort. Durch die gleichmäßige Gewichtsverteilung wird eine einfache Handhabung auf nebenem Gelände gewährleistet, während die präzise Steuerung und hohe Zuverlässigkeit für maximale Effizienz sorgen.
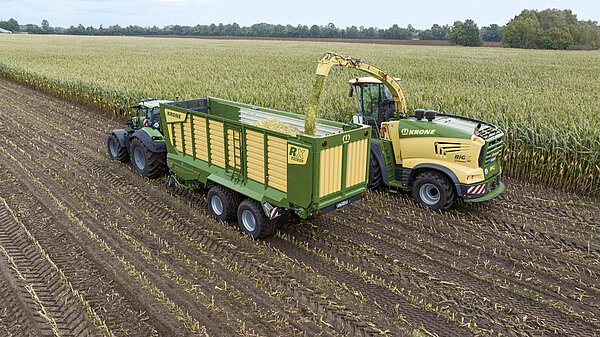
The forager filled RX 360 GL/GD: The sturdy steel structure and the high 20 t gross axle weight rating make the RX 360 a dependable and costeffective silage trailer in the haulage fleet that supports the forage harvester.
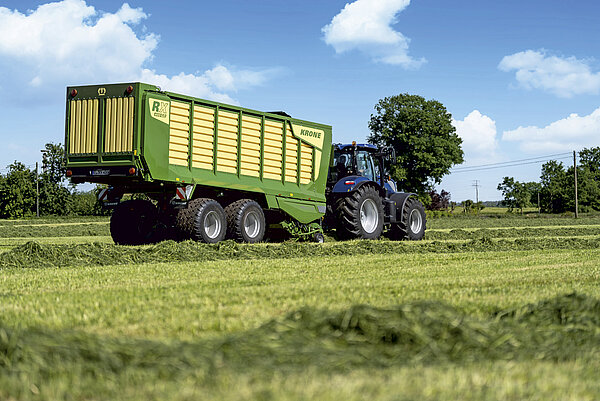
The self-loading RX 360 GL/GD: The wide pick-up and cut-and-feed rotor feed the material effectively through a short feed chamber and across the full width of the load area. Arranged in close proximity to the wide rotor tines plates, the blades on the cutting system give scissor-like cuts.

- Clean cut in theoretical length of 28 or 37 mm
- Optimal structure gentle conditioning under all conditions
- Homogeneous uniform conditioning of each stalk over its full width
- Precise wide steel plates and blades arranged for shear cutting
- Perfectly coordinated precise interaction between pick-up and cutting rotor
- Innovative new integral rotor with unique divider wall system
Thanks to the KRONE OptiGrass system, the forage quality is clean, homogeneous and uniform. This is possible due to the precise cutting method with a choice of cutting lengths of 28 or 37 mm. Thanks to the perfectly coordinated technologies, conditioning is gentle, resulting in a clean and high-quality result.
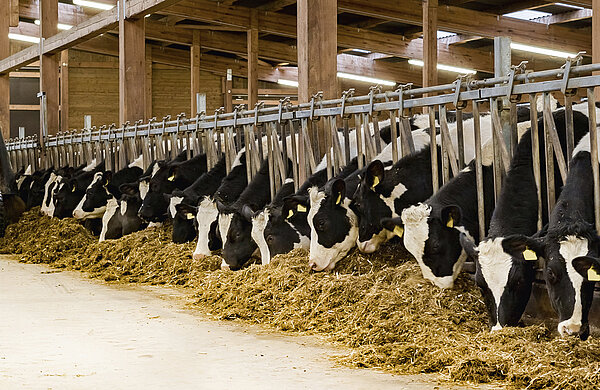
The right quality on the forage table is the key to success in the cowshed. A high-quality basic forage ensures that the animals have access to sufficient amounts of nutrients and vital trace elements. A high intake of tasty and quality forage is the foundation for successful milk production and the best possible health of your herd.
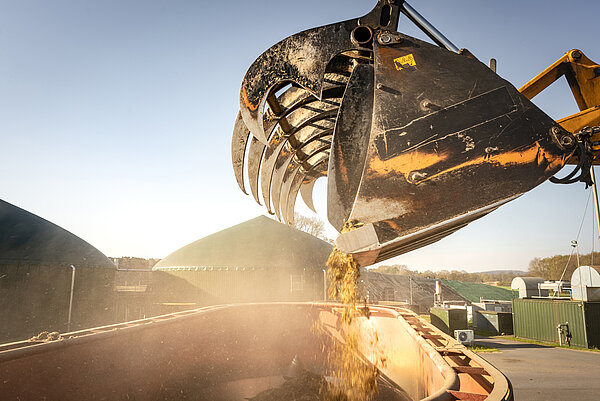
OptiGrass for optimum TMR, with the two cutting unit variants (28 mm or 37 mm) the structure value can be adjusted variably which enables the built-in blade group control system to double the cutting length if required. Our goal: short, structured and homogeneous basic forage, perfect for total mixed rations. Result: best forage presentation, low selection and minimised residual amounts on the forage table.

The KRONE OptiGrass concept redefines homogeneous forage. Conditioning of every blade of grass was the ultimate development goal. Homogeneous forage, on the one hand, contributes to improved preservation as it is less susceptible to mildew and other types of spoilage. Furthermore, the uniform quality and composition of the silage enables precise feeding which meets all the needs of your herd.
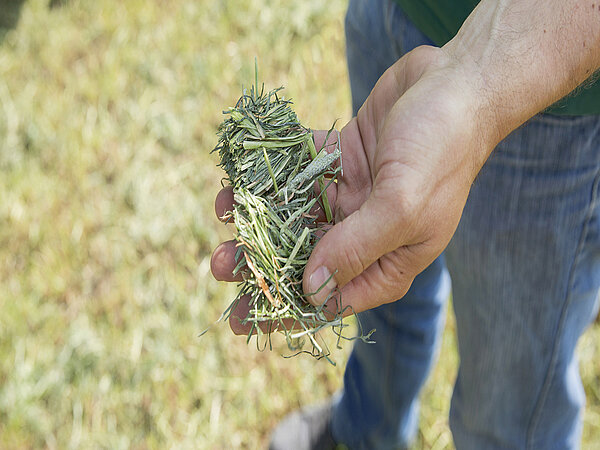
A very important aspect is the optimal structure of the forage; this helps to support the natural chewing and digestive activity of the animals and reduce the risks of constipation and digestive problems. Well-structured forage promotes natural utilisation and therefore the milk production of your animals. The KRONE OptiGrass concept ensures crunchy, well-structured forage and prevents the crop from being crushed at any time of the year.
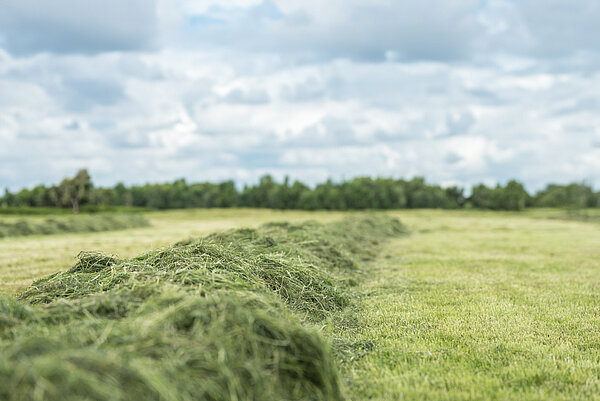
A high milk yield is the decisive factor for the economic success of a farm. The forage intake required for this is ensured in particular by tasty and pure forage. To ensure clean pick-up without the introduction of raw ash, fungi and yeasts, the OptiGrass concept with its wide oscillating pick-up and excellent scanning characteristics offers the right technical solution to achieve perfect crop pick-up.
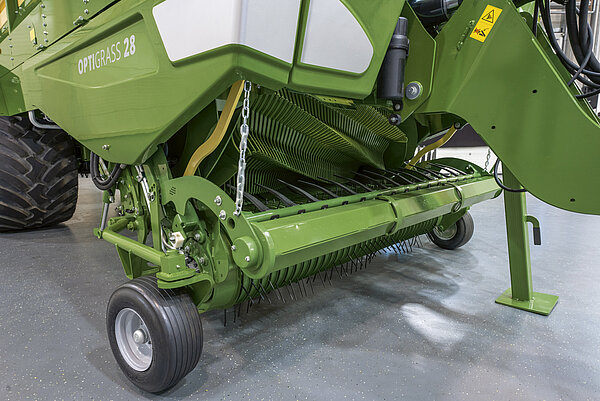
- Hydraulic drive separated from the feed and cutting rotor
- Automatic and manual speed control to adapt to the current ground speed
- Maintenance-free and hard wearing
- Consistent collection of the material by tines in a staggered W arrangement
- Large pivoting range
- Electrohydraulic suspension for even better sward protection.
The EasyFlow pick-up with hydraulic drive is the ideal solution for demanding requirements. With its 6.5 mm thick double tines in a helical layout, it meets the most demanding requirements in ease of maintenance and pick-up capacity. The hydraulic drive integrated in this pick-up offers an even larger work width, which helps to collect even more material at an optimum driving speed and maximizes the intake capacity.
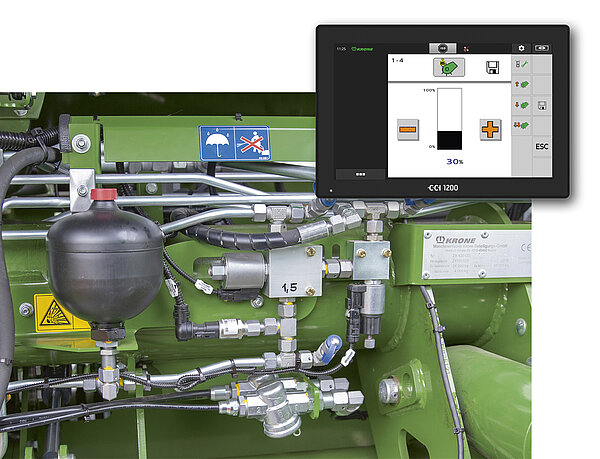
A nitrogen damper provides electro-hydraulic suspension for the pick-up for even better soil protection. The system allows operators to set the suspension pressure from the cab and on the move.
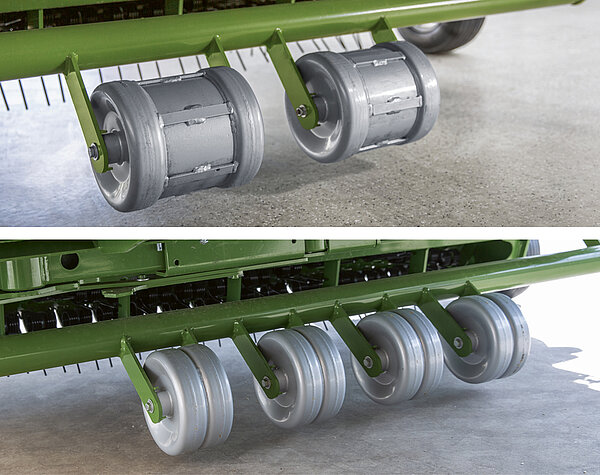
Wide guide wheels behind the pick-up ensure clean forage intake on damp ground. The height-adjustable wheels prevent them from sinking too deep and therefore protect them from damage. The 28 mm OptiGrass cutting unit has four wheels, the 37 mm cutting unit has two.
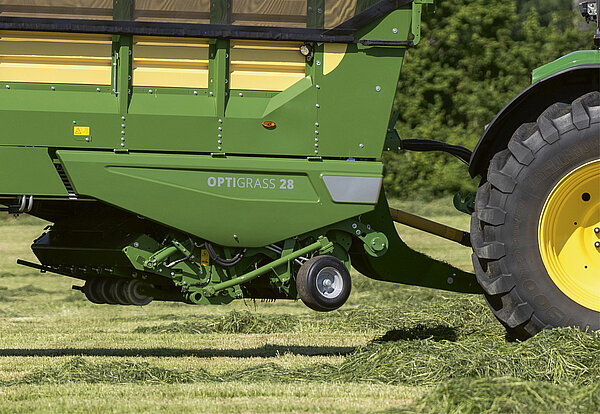
The articulated drawbar with double-acting ram is standard specification and provides a generous ground clearance of up to 75 cm – enough to roll on clamps no problem. The new automatic articulated drawbar offers a better ground clearance for headland turns. One headland and one road position can be programmed to the control unit.
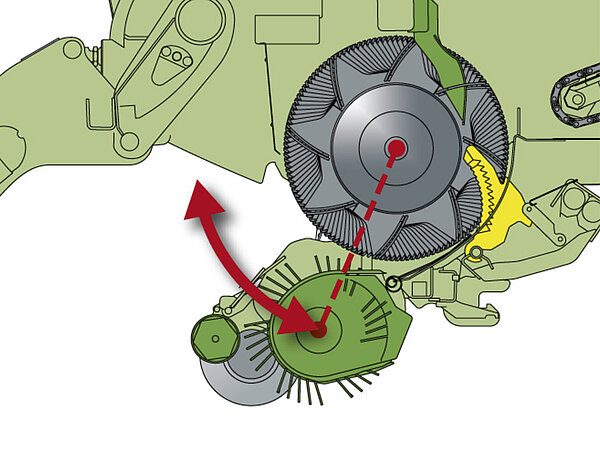
In undulating terrain, the pick-up oscillates through a constant range around the core of the cutting rotor, maintaining an optimum flow of material into the machine no matter how difficult the conditions. The steering is aligned with the centre of the cutting rotor, enabling a wide lift height – ideal on the headland.
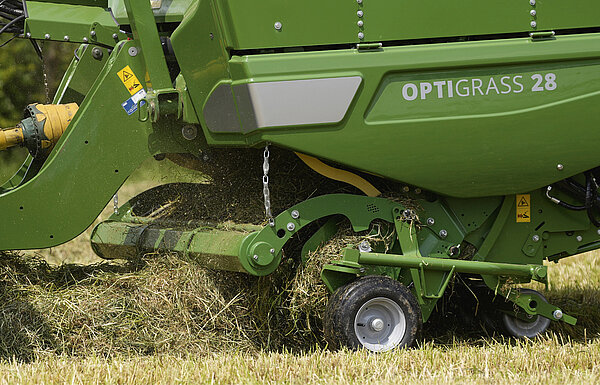
The laterally pivoting pick-up follows ground contours both axially and transversely and benefits from more generous travel now – courtesy of the integral hydro motor that replaces an external sprocket. The result is a clean rake and nothing is left behind.

The pneumatic guide wheels on either side of the pick-up offer height control for full adaptation to any ground contours. Tracking excellently behind the tractor during headland turns, these wheels avoid scuffing and offer best protection of the sward.
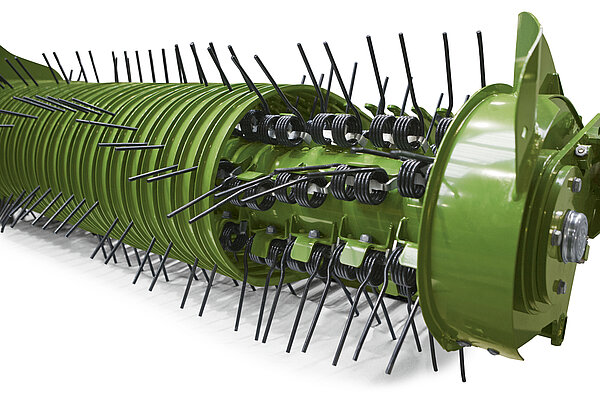
The 6.5 mm tines with large-diameter coils withstand the most arduous conditions.
The integral hydro motor offers a number ofadvantages:
- It frees space on the pick-up ends for a wider work width
- Maintenance-free
- The absence of sprockets on the sides translates into a larger pivoting range
- Manual or automatic ISOBUS speed adjustment to the current ground speed and prevailing conditionss

Arranged in a W, the tines warrant a consistent crop flow and an equally consistent and fullwidth supply of the material to the rotor cutter, boosting throughputs and machine fills.

KRONE had good reasons for opting against cam track controlled tines on the EasyFlow pick-up. Instead of using many moving parts that are prone to wear, we rely on special strippers that ensure the pitch of the tines is always correct and their working width always ideal. The 6.5 mm diameter tines with large coils are particularly hard-wearing. Six rows of tines arranged in a wavy pattern ensure there is always the same number of tines in work, which eliminates load peaks and spreads the material consistently across the full working width.
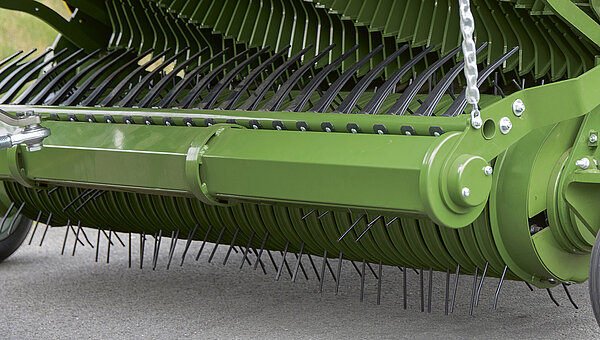
Offering a work width as wide as 2 m, the EasyFlow pickup effectively gathers even wide swaths and feeds the material in an extraordinary consistent flow to the feed rotor. Pivoting and spring-loaded, EasyFlow provides perfect ground contouring even in very rough terrain.
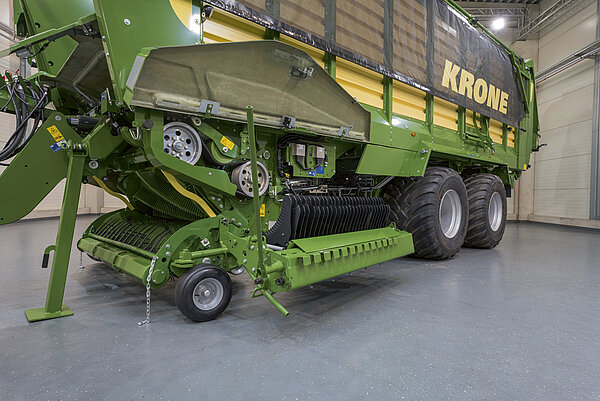
- OptiGrss 37 mm cutting distance with 40-blade cutting unit
- OptiGrass 28 mm cutting distance with 54-blade cutting unit
- KRONE PowerBelt the drive concept for extremely high throughput rates.
- Integral rotor with augers high-performance crop flow with maximum pick-up width
- KRONE SplitCut optimum conditioning over the entire rotor width
KRONE OptiGrass – state-of-the-art technology for perfect forage conditioning. The 40-blade cutting unit with a cutting distance of 37 mm and the 54-blade cutting unit with a cutting distance of 28 mm ensure optimum forage quality. KRONE PowerBelt ensures extremely high throughput rates and the KRONE SplitCut system ensures gapless conditioning across the entire rotor width.
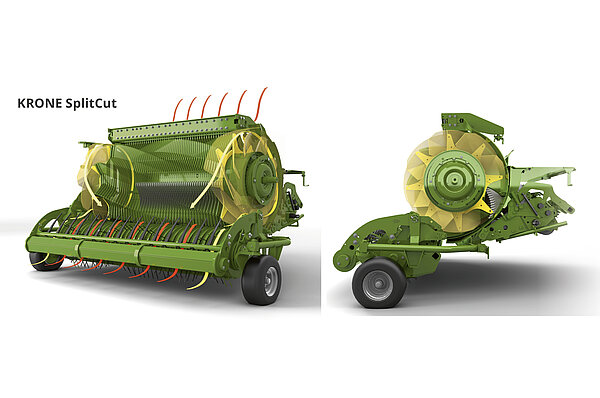
A concept which, thanks to its innovative design, enables optimum conditioning of the forage across the entire width of the rotor. Consisting of a cutting blade, a divider wall, scraper tines and crop deflector sheet, the two SplitCutters ensure that the crop is separated at the cutting blade and fed back centrally into the crop flow. This ensures that every stalk has completely passed through the cutting blades, resulting in perfect conditioning quality.
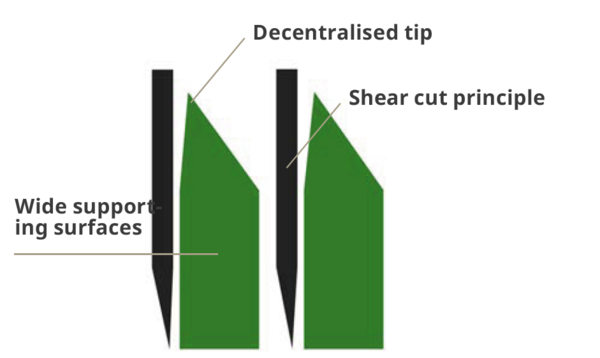
Precise shear cutting is made possible by the use of extrawide steel plates in combination with a dense arrangement of blades and supporting surfaces. The width of the supporting surfaces varies between 17 mm and 22 mm, depending on the cutting unit. The decentralised arrangement of the tips of the supporting surfaces creates an optimum shearing effect on the blade, resulting in the crop being picked up gently and with little effort. This prevents mushing.
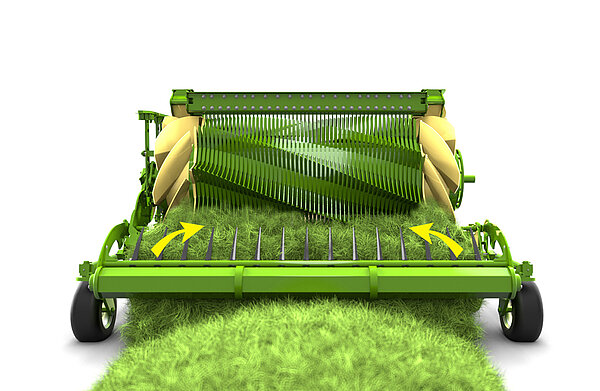
The new integral rotor concept combines numerous advantages and significantly improves the performance of the cutting system. The 22 cm wide auger bodies, which are part of the cutting rotor, ensure that the crop is transported evenly and cleanly to the centre of the rotor. This results in a powerful crop flow with maximum pick-up width and, at the same time, the best possible cutting quality thanks to optimum pre-compression in the conveyor pockets. The concept, in conjunction with the enormous diameter of the cutting rotor, enables the RX to achieve maximum throughput with optimum conditioning quality. 1. The entire swath is picked up via the wide pick-up 2. The auger body conveys the grass from the outer areas to the centre of the rotor. 3. The material is compacted in the rotor pockets and formed into a perfect cut package.
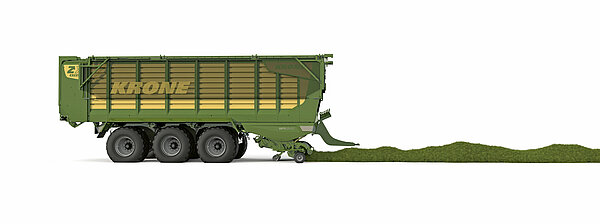
Maximum throughput rates and high loading speeds allow hardly any errors. In practice, however, uneven swaths with changing crops are more common. Thanks to the powerful KRONE Powerbelt, these short-term load peaks are cushioned and the overload protection is prevented from tripping. With the KRONE Powerbelt you can drive on while others stand still.
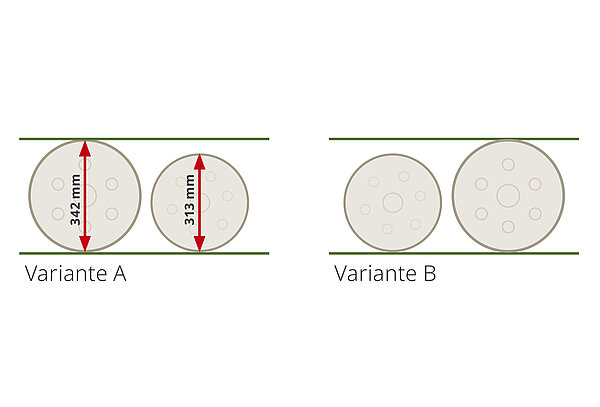
The unique speed concept of the loading and forage transport wagon offers different rotor speeds with specific advantages depending on the position of the pulleys:
- Variant A: This configuration is optimal for large emergence rates and voluminous swaths in spring. A rotor speed of 47 rpm is used here to achieve maximum throughput with optimum compression.
- Variant B: A rotor speed of 40 rpm ensures good throughput rates and perfect pre-compression. This configuration is ideal for lower emergence rates in late summer and autumn and for smaller tractors where throughput is limited.
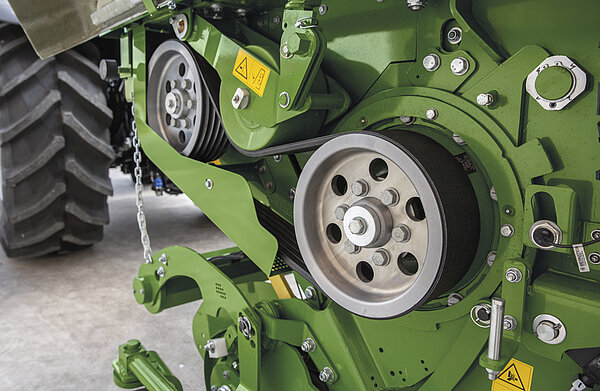
The KRONE Powerbelt drive concept supports the rotational speed reduction from the main drive to the cutting rotor by means of a planetary gearbox located in the rotor. The compact design of the assembly allows us to maximize the length of the rotor and hence the width of the crop flow. The drive is impressive thanks to its high throughput, extremely quiet running, low wear and minimal maintenance. A wide belt enables power transmission of up to 430 hp in the drive train. A cam clutch in the main universal shaft ensures the safety of the entire drive train up to a torque of 3000 Nm.
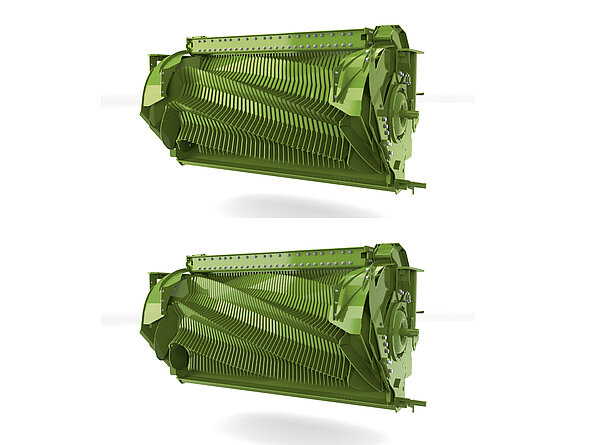
With the OptiGrass system, the RX series offers two cutting unit variants with theoretical cutting lengths of 28 or 37 mm. The integral rotor concept, which cuts more precisely and shorter than ever with fewer blades, ensures compact cut packages. Combined with the EasyFlow pick-up, the Opti-Grass cutting rotor and SpliCut edge-cutting system, the KRONE RX delivers an optimum result in all conditions.
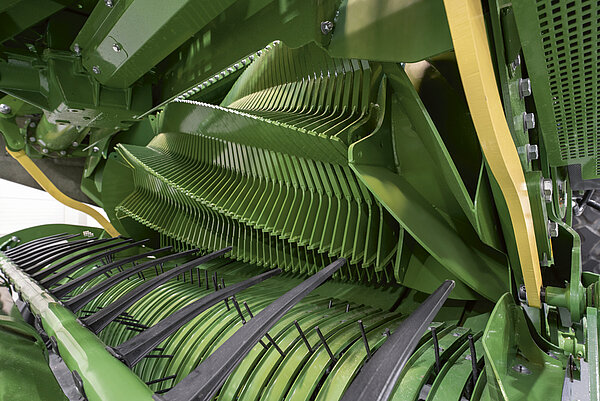
The new high-performance 'OptiGrass' cutting unit systems take forage quality to a new level. In addition to a theoretical cutting length of 37 mm with a maximum of 40 blades, it is now possible to achieve a cutting length of 28 mm with a maximum of 54 blades. Together with the KRONE SplitCut, nothing stands in the way of optimum forage recovery. With the optionally available SpeedSharp blade grinding device, sharp blades are guaranteed everywhere and at all times!
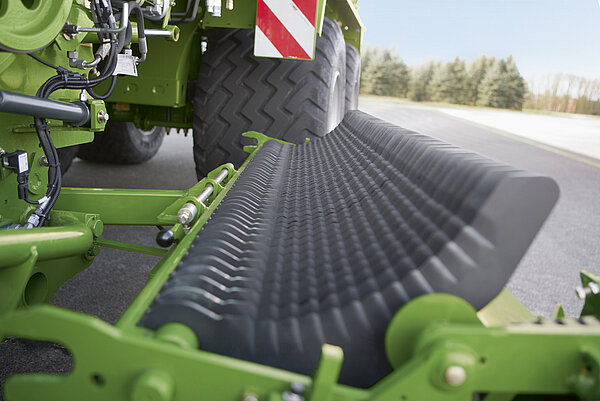
- Top cutting quality Shear cut
- Theoretical cutting length: OptiGrass 28 mm with maximum 54 blades | OptiGrass 37 mm with maximum 40 blades
- Central blade group control system: 0, 20, 20, 40 blades | 0, 27, 27, 54 blades
- Blade changing without tools and with central locking
KRONE OptiGrass cutting units offer wide tine holders and closely spaced, guarded blades which provide an easy and precise cut, similar to a pair of scissors. Two cutting units with 40 or 54 blades are available for optimum conditioning. Thanks to the central blade group control system, the cutting length can be varied at any time between a half and full set of blades, allowing cutting distances of 28 or 56 mm or 37 or 74 mm. OptiGrass therefore offers a flexible solution for different cutting lengths.
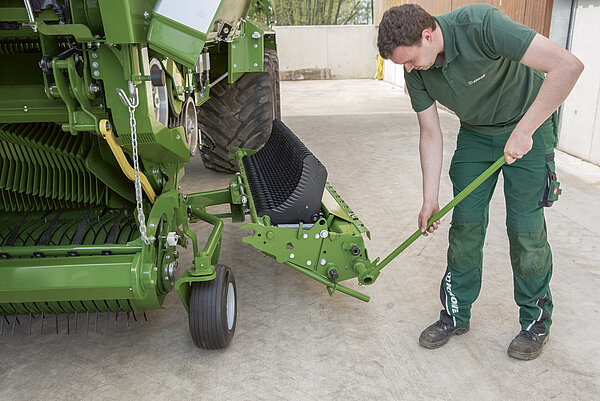
The desired cutting length can be set quickly and easily via the central blade group control system. With the ZX, theoretical cutting lengths of 28 or 56 mm with 54 blades and 37 or 74 mm with 40 blades can be achieved. In the zero position, the crop remains uncut.
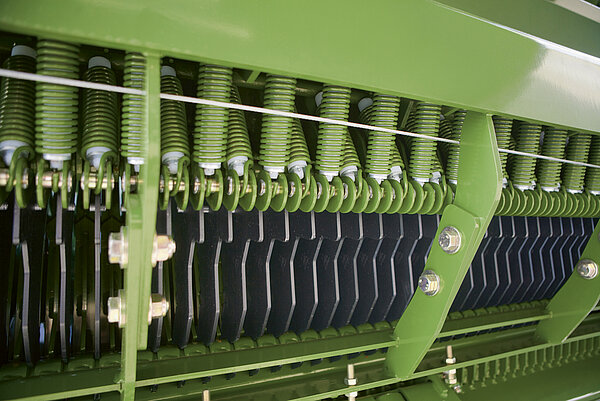
Equipped with individual spring protection, each blade retracts and swings back automatically once the foregn object has passed. The tripping force is set variably from the cab and can be adjusted to special conditions.

The blade cassette lowers hydraulically to remove a blockage. After the blockage has been removed, the blade cassette is swivelled in again and work can be resumed immediately.

The crop cannot escape the blades because the distance between the blade and the wide supporting surface of the conveyor rotor tine and its asymmetrical tip is very small. The result: perfect cutting quality through and through, no squeezing, no mushing.
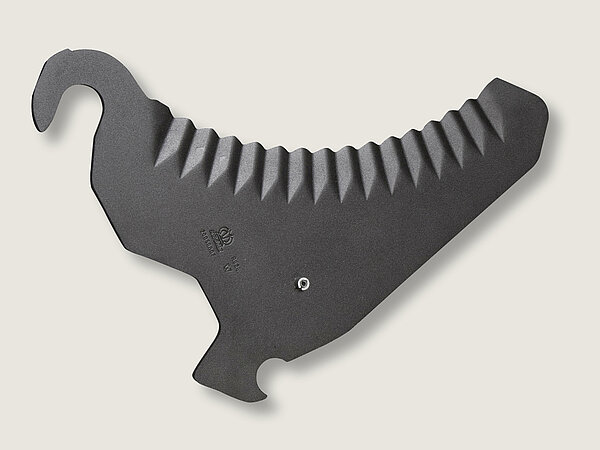
Cutting with their full edges, these blades lead to smoother and quieter running. The wavy blades maintain their sharpness over extended periods of time.
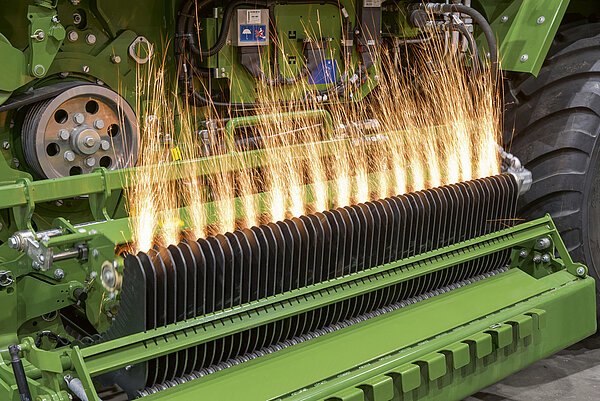
- Sharpens the blades conveniently and fast within minutes
- Simultaneous sharpening of half (OptiGrass 37) or a third of the blades (OptiGrass 28)
- No annealing of the knifes thanks to a 'cold grind'
- Simple design, absolutely dependable
- No sparks flying under the wagon
Sharp blades are fundamental for clean and smooth cuts. Therefore KRONE developed SpeedSharp, the unique blade sharpening system for fastest, safest and most convenient grinds. The trademark of this system is its simplicity.
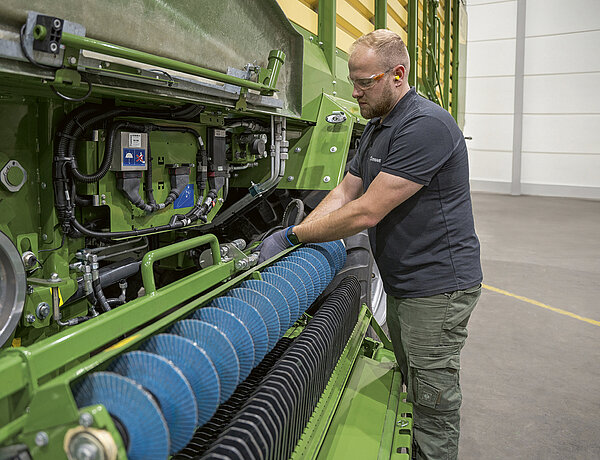
Simply swing out the blade cassette, fold up the grinding shaft, couple two oil hoses and connect an electric lead. Then press an external control to start grinding hydraulically and watch how the shaft moves automatically up and down and to the sides, completing the job without any interference from the operator. The grinding is carried out with the blade cassette out and alongside the machine so you can easily watch the process.

A complete grinding process, including swivelling the cutting unit out and in, is quickly completed: In just five minutes, all 40 or 54 blades are sharp, depending on the number of grinding cycles. With the blade cassette out and alongside the machine, the operator can watch the grinding process and conveniently check on the result.
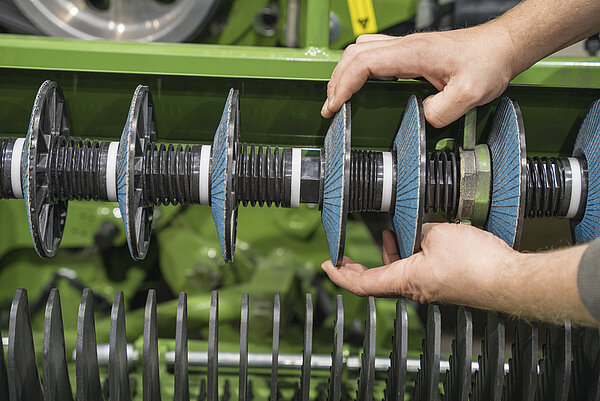
Each disc is pressed on to the blade by a bevel spring, a design that leads to a high-quality and consistent cut of all blades whilst minimising the material that is removed from each blade. The system warrants consistently sharp blades even when these show different degrees of wear.
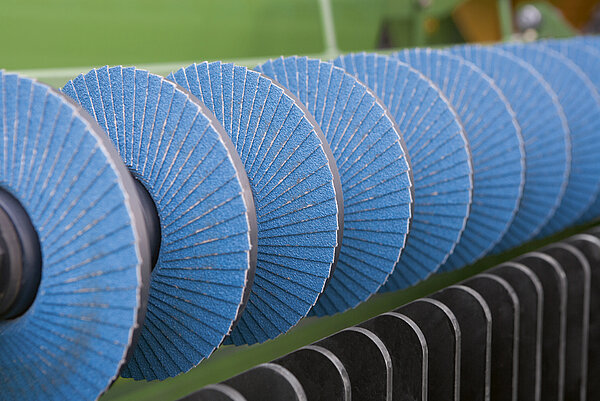
Depending on the number of blades, grinding is carried out with 18 or 20 flap discs which, with individual, widely overlapping grinding flaps, ensure a particularly high grinding performance and a long service life. give a 'cold' grind that prevents the blades from annealing.
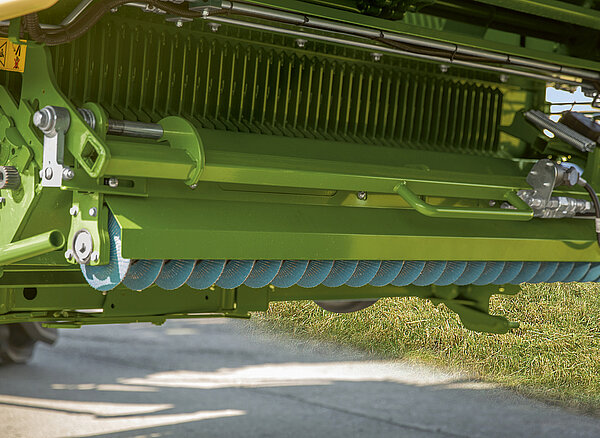
The grinding discs of the optional fully automatic grinding device are arranged on a laterally movable and hydraulically driven shaft. All work processes for grinding the blades are carried out automatically at the touch of a button.

They can set the blade grinding interval on the terminal to adapt the intensity to the actual level of wear.
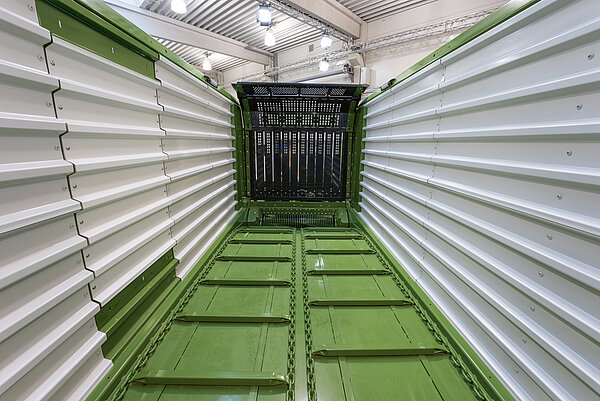
- All-steel floor and all-steel body
- Choice of headboards: pivoting or top hatch
- Double scraper conveyor, sloping towards the front
- Robust round steel chains with closed cross tubes
- Standard LED light bars illuminate the load area
- Integrated filling level indicator in the operating terminal
- 3 discharge rollers with large diameter (47 cm) as standard
With their all-steel loading space, the RX dualpurpose loading and forage transport wagons are designed for the toughest practical applications. Choose a pivoting headboard or a rigid headboard with a top hatch to optimize the machine's filling capacity. The robust scraper conveyor empties
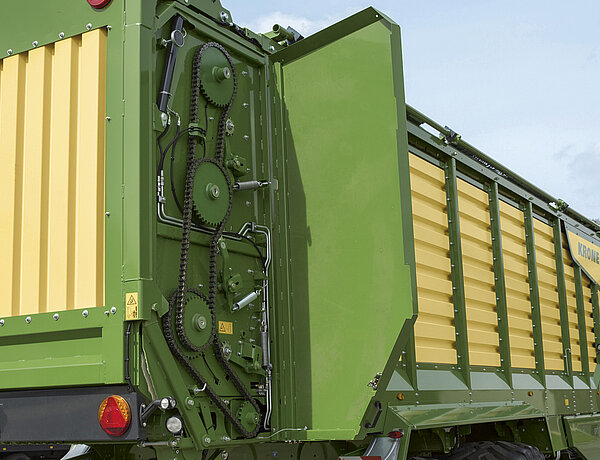
[Translate to EN:] Die besonders robusten Getriebe und die 1 Zoll starken Rollenketten mit automatischen Kettenspannern übertragen die volle Leistung. Der Kettenantrieb erfolgt von einer längs im Fahrzeugrahmen liegenden Welle und über ein im Seitenträger geschütztes Winkelgetriebe.
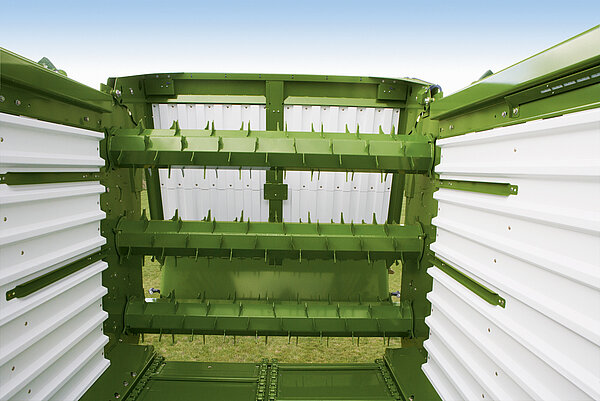
[Translate to EN:] Mit drei geschlossenen Dosierwalzen und einstellbarer Rückwand legen Sie einen noch homogeneren Futterteppich ab. Die v-förmig angeordneten Zinken verteilen das Futter über die komplette Breite. Die höhere Drehzahl der Dosierwalzen führt zu noch kürzeren Abladezeiten.
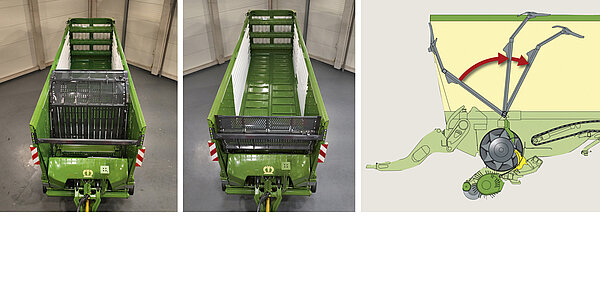
The RX 400 and RX 430 models have a hydraulic headboard which pivots to various positions to support the fi lling process. For example, when the machine is fi lled by a forage harvester, the headboard pivots all the way forward to maximize the capacity and cut out the risk of losses. By comparison, when the machine is gathering material through the pick-up, the headboard is nearly vertical to optimize the fi lling process. Once the load area is fi lled, the headboard pivots towards the tractor to expand the load area by 4 m³, simply by using the space above the rotor. This way the RX runs much closer behind the tractor than other wagons of the same capacity. To speed up unloading, the headboard can pivot back and forth and support the work of the fl oor chain.

- Tandem compound running gear, 18 t for RX 330 and RX 370 as standard
- Hydraulic 20 t tandem chassis: RX 400 as standard | RX 330 and 370 optional
- Hydraulic 27 t tridem chassis optional for RX 400
- Narrow and compact drawbar
- Articulated drawbar for high lifting height
- Intelligent self-steering as standard
- Contactless electronic forced steering, optional
Varying harvest conditions, difficult situations on the clamp, high payloads, and long-distance travel at speed call for a running gear and a drawbar that offer maximum strength and stability as well as superior comfort and safety to the operator. With ball-head attachment 80, articulated drawbar and tandem or tridem chassis as well as adjusted tyres, the RX dual-purpose loading and forage transport wagons are perfectly equipped for all applications.
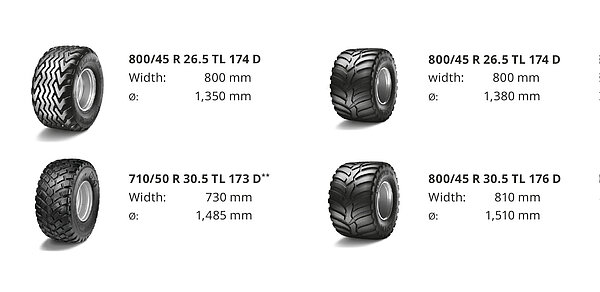
The optional 30.5" tyres stand for increased load capacity and low drag resistance, sward protection and transport safety.
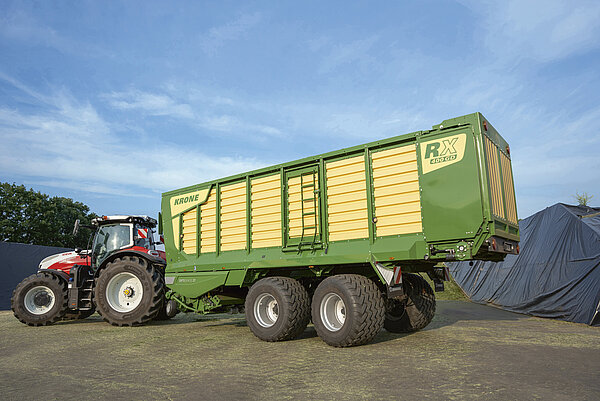
Steered rear axle:A mechanical forced steering system is available as an option on the rear axle.The steering rod makes headland turns easier, reduces scuffi ng and tyre wear. It is easily unlocked for quick attachment and removal. The forced steering system is set up and controlled with the help of pressure gauges. An electronic forced steering system is available as well, which allows operators to intervene and counter drifting in sloping fi elds or on the clamp for example.

The rear and front axles in the tandem assembly are levelled hydraulically to ensure a uniform weight distribution at any time as well as an optimum ride and stability in undulating terrain. A range of tyre options is available to suit all harvest conditions. Sloping mudguards prevent crop from collecting here.
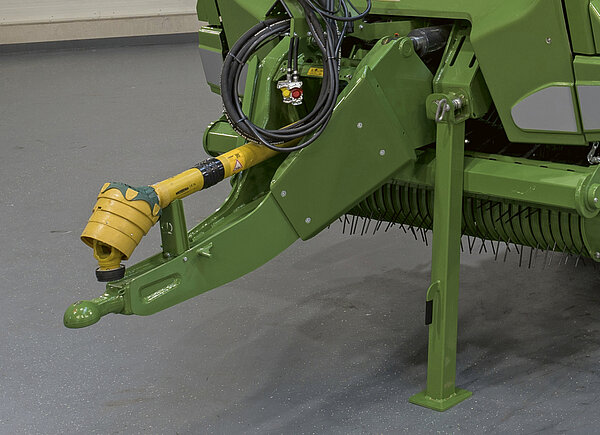
Drawbar: Their long and slim drawbar gives the RX models extra agility for manoeuvring in tight turns. The articulated drawbar has a standard suspension system that absorbs shockloads and offers maximum operator comfort, whilst two massive rams raise the laden machine and increase its ground clearance on the clamp. An optional automatic system stores and retrieves the two drawbar positions automatically.
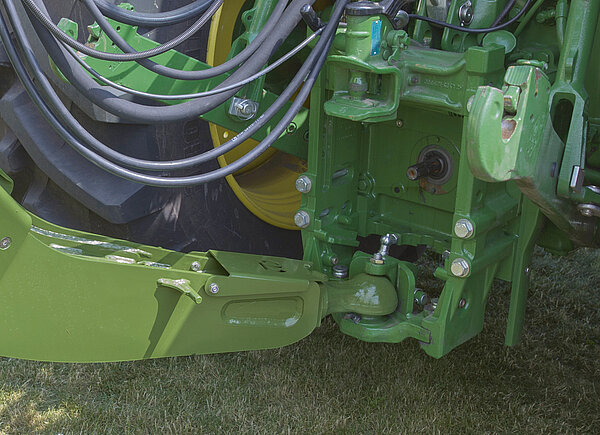
All RX models hitch to a bottom-mount 80 ball. Approved for tongue loads of up to 4 tonnes, these machines offer great agility at minimum wear.
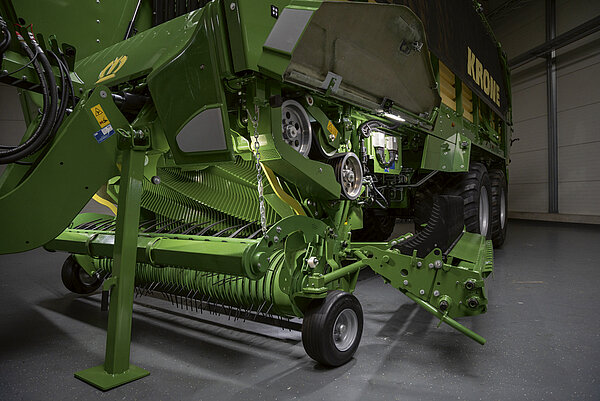
- Premium lighting package as standard
- Excellent all-round visibility at night thanks to two powerful LED working lights at the rear
- Safe in the field and on the road with front position lamps and reflectors
- The load always in view Thanks to LED light strips installed as standard in the loading space
- Two additional working lights can be quickly retrofitted thanks to prepared cable position
The KRONE RX's Premium lighting package not only enhances safety, but also increases nighttime productivity. The Premium package provides optimum lighting of the surroundings, the loading space, the crop flow and the drive components. Additional working lights can be retrofitted as an option.

Four powerful LED light strips are fitted as standard in the loading space to facilitate working in the dark. With its two working lights at the rear, the KRONE RX provides optimum illumination of the surrounding area. For ideal illumination of any working environment, two additional freely positionable working lights can be mounted at the front or rear. The cable position required for this is prepared as standard in the RX to enable simple and quick assembly. Two modes can be used to conveniently configure field and discharge lighting.
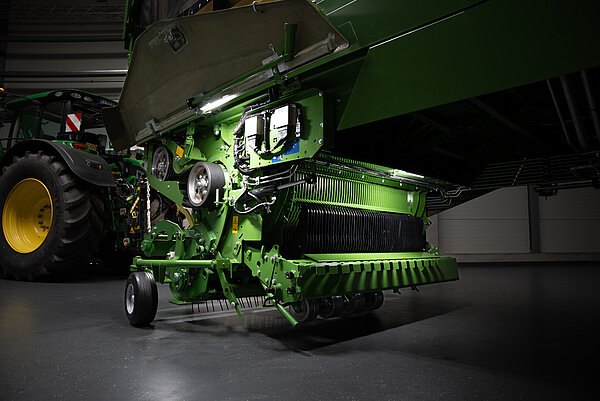
An LED strip located under the side guard provides optimum illumination of the drive components and the swung-out blade cassette. In addition, the lighting of the feed channel ensures straightforward handling when swivelling the blade cassette in and out.
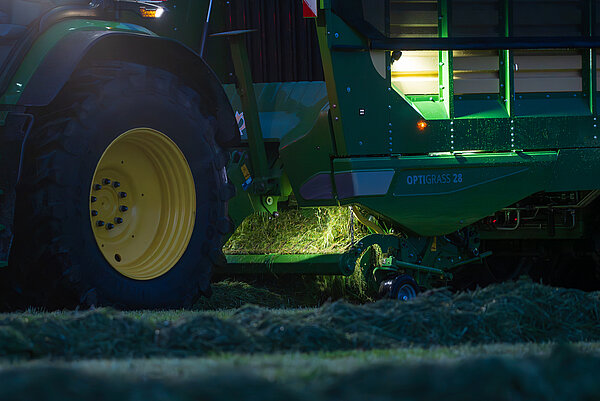
Two LED strips on both sides provide optimal lighting in the area of the crop intake. They provide sufficient illumination in front of and behind the pick-up and, thanks to their diffuse light, create a pleasant working atmosphere without dazzling.
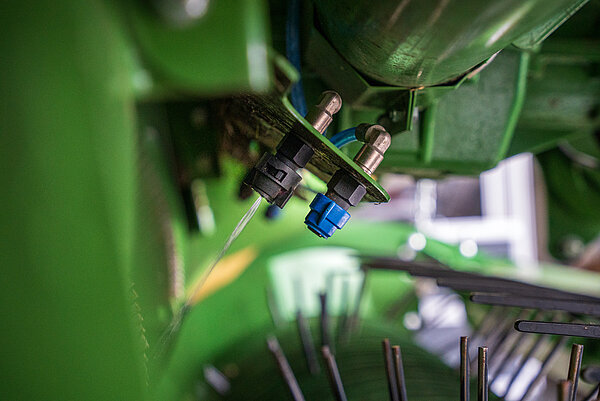
- Spreading above the pick-up using flat jet nozzles
- 200 litre tank capacity optimally positioned for access at the rear
- Easy cleaning of the system
- Removal of the pump unit without tools
- Convenient operation via the terminal
- Different modes for optimal dosage
The KRONE RX has an integrated dosing system with a 200-litre silage additives tank which can be operated in different modes. The pump unit, including the filters and valves, is installed in the rear of the vehicle to save space. An electronic filling level indicator enables reliable and fast monitoring of the silage additives supply.
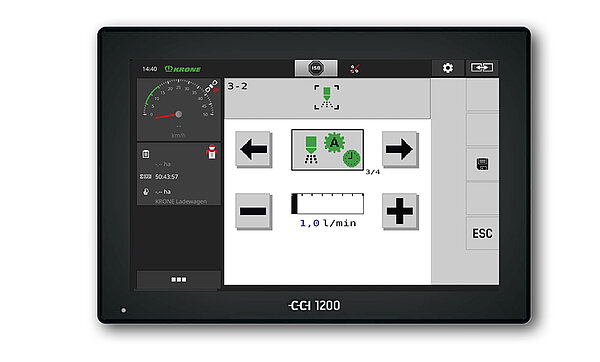
The dosing system is fully integrated into the user interface of the RX and can be operated in different modes. Whether a fixed dosing rate (l/min), a dosing rate-dependent dosing rate (an optional weighing device is required for this) or a percentage flow rate – all values can be set easily and conveniently in the submenu.
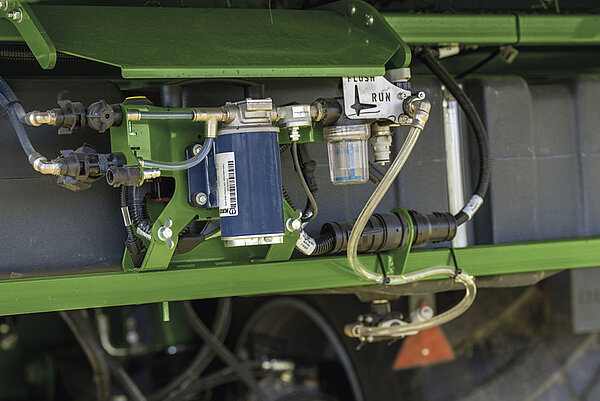
The pump unit, which includes filters and valves, is installed in the rear of the vehicle to save space. It can be easily removed without tools, for example to protect it from frost in winter. Practical functions, such as a compressed air connection for emptying the lines, have also been considered. To carry out maintenance work, the pump can be switched by a push button.
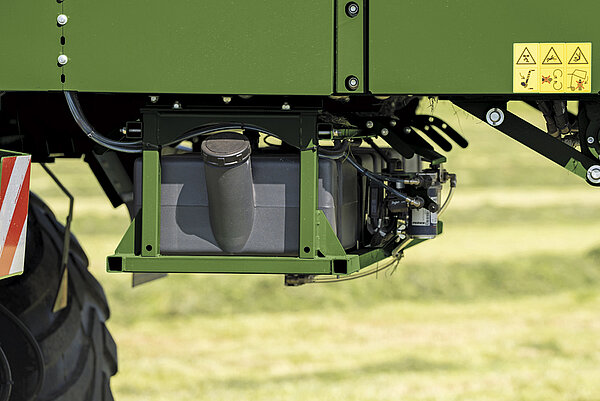
The KRONE RX features a 200-litre silage additives tank which is optimally positioned for access behind the rear of the vehicle. Thanks to two side openings, the tank is easy to clean. The electronic filling level indicator on the terminal enables quick and precise monitoring of the filling level at any time.
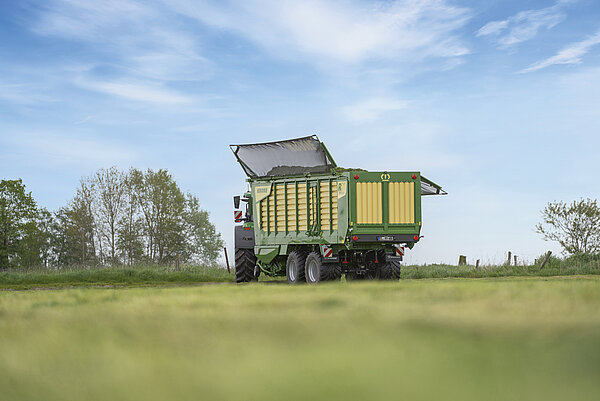
- Loading space cover for loss-free transport
- Camera with colour display on the monitor
- Weighing device for an exact measurement
- KRONE SmartConnect telemetry unit optimal data management
The loading space cover ensures clean transport even when driving fast and increases safety in road traffic. A camera helps to see the working environment better, making work easier and safer. The electronic weighing device can be used to measure the loading quantity precisely. The KSC control unit ensures rapid transmission of the recorded data.
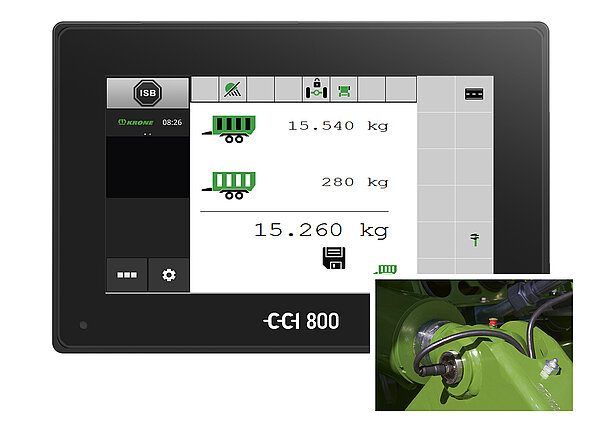
The electronic weighing system uses sensor pins inside the drawbar and on the tandem/tridem axle with hydraulic levelling. The system determines the weight of the load by computing the difference between the gross weight and the weight ofthe material left on the machine after unloading is completed.
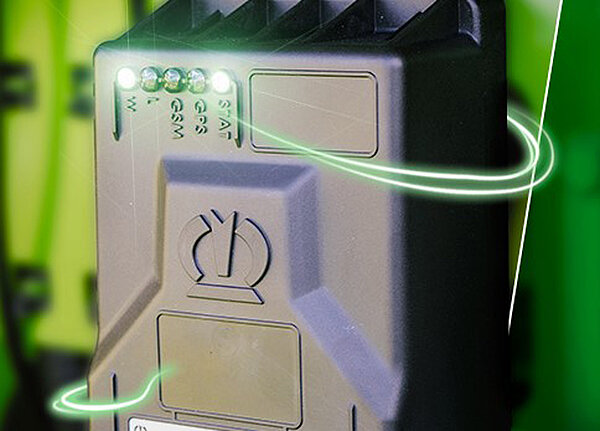
The ZX can be optionally equipped with the KRONE Smart-Connect telemetry unit. This interface is used with GPS and WLAN function as the basis for data management. Telemetrics allow managers to track the wagon and record all major data and transmit them to the office. This is the modern way of farming.
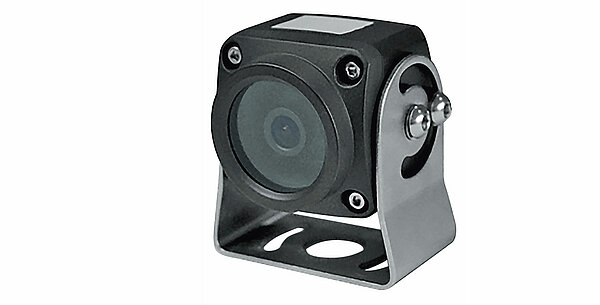
An optional camera is available for all ZX models. The images are displayed on the colour screen for added visibility and safety.
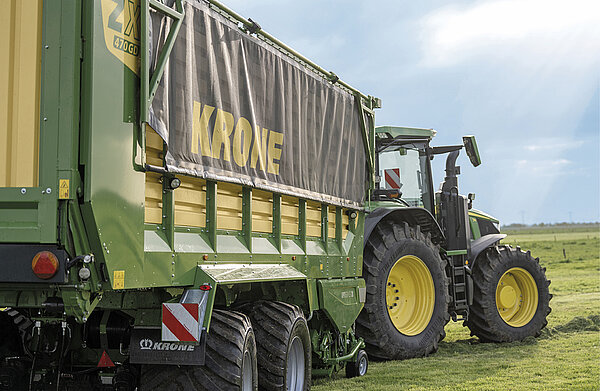
The covers are operated by hydraulic motors for quick and dependable control.
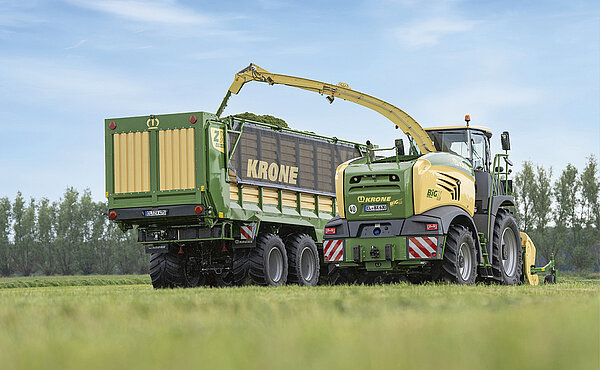
When the loading space cover halves are folded down to the side, the ZX is easy to load from the forage harvester. There is nothing in the way that might obstruct filling.
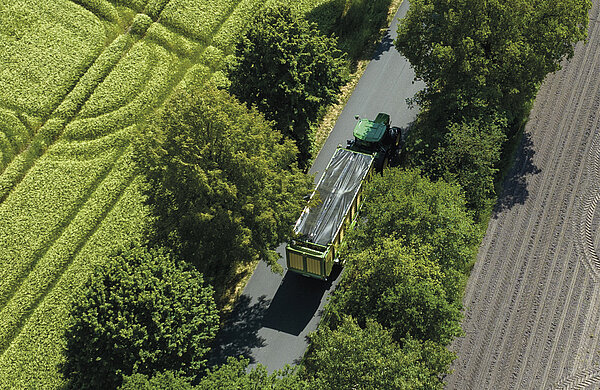
The optional crop covers are flexible to adapt to the contours of the forage mass. Hinged to the sides, they cover the material effectively and will not open as the combination travels at speed.
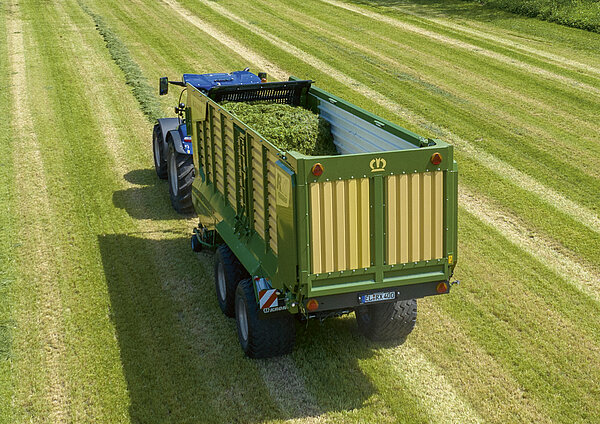
- Convenient for operators
- Clear concept
- Easy
- CCI ISOBUS – one control box for all
Operator comfort is essential. Our shockproof operator terminals are compact, clear-cut and easy to operate. They feature backlit buttons to reduce operator fatigue during those long shifts well into the night. The CCI terminal is a universal operator control unit, which is compatible with a wide variety of ISOBUS implements from many manufacturers.
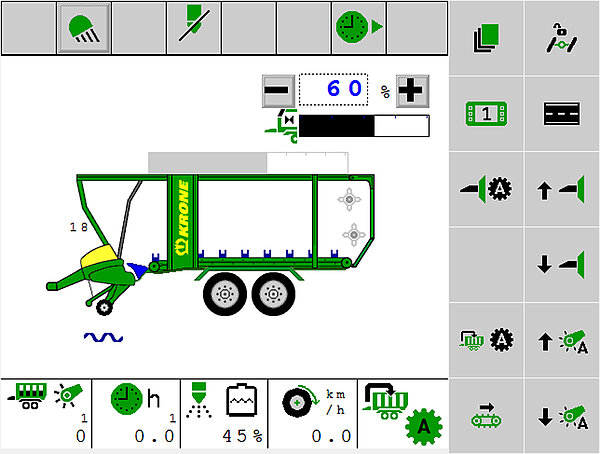
The user interface of the KRONE RX is particularly user-friendly thanks to its simple and intuitive operability. Various work steps are illustrated by visualisation, such as rotating discharge rollers. More comfort is provided by the configurable display bar which can be used to individually adjust the user interface to the user's requirements. Automatic functions, such as the PowerLoad automatic loading system, the automatic unloading system and the drawbar control system, are also available.
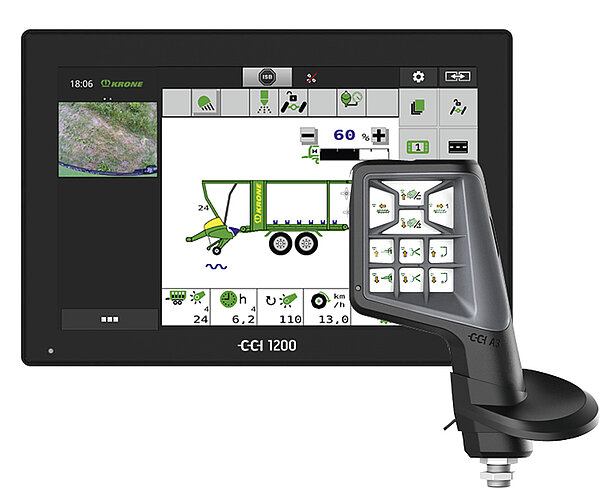
The two operator terminals CCI 800 and 1200 with 8″ or 12″ touch display allow users to split the screen for example to see all machine control elements in one view and the camera footage in the other. Also, an additional AUX joystick enhances operator comfort even further.
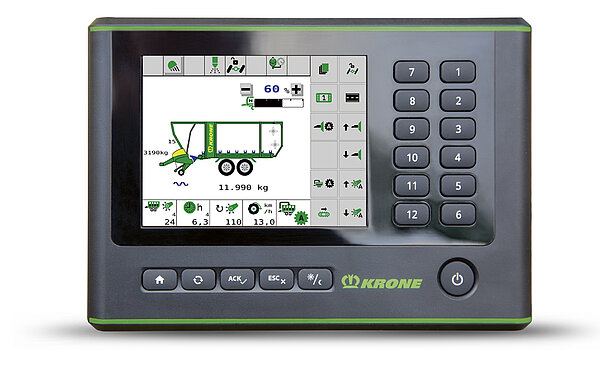
The compact DS 500 terminal has a 5.7-inch colour display screen can be operated with 12 function keys, the touchscreen or the scroll wheel on the back. An optional joystick is available for even more convenient operation.
Models
RX 330 GL | RX 330 GD | RX 370 GL | RX 370 GD | RX 400 GL | RX 400 GD | ||
---|---|---|---|---|---|---|---|
Designation | loading and forage wagon | loading and forage wagon | loading and forage wagon | loading and forage wagon | loading and forage wagon | loading and forage wagon |
configure
|
Capacity (m³) | 33 | 33 | 37 | 37 | 40 | 40 |
configure
|
Pick-up working width (m) | 2.12 | 2.12 | 2.12 | 2.12 | 2.12 | 2.12 |
configure
|
28 | 28 | 28 | 28 | 28 | 28 |
configure
|
|
No. of discharge rollers | - | 3 (2) | - | 3 (2) | - | 3 (2) |
configure
|
Power requirement (kW/hp) | 130 / 175 | 130 / 175 | 130 / 175 | 130 / 175 | 130 / 175 | 130 / 175 |
configure
|
configure
|
configure
|
configure
|
configure
|
configure
|
configure
|